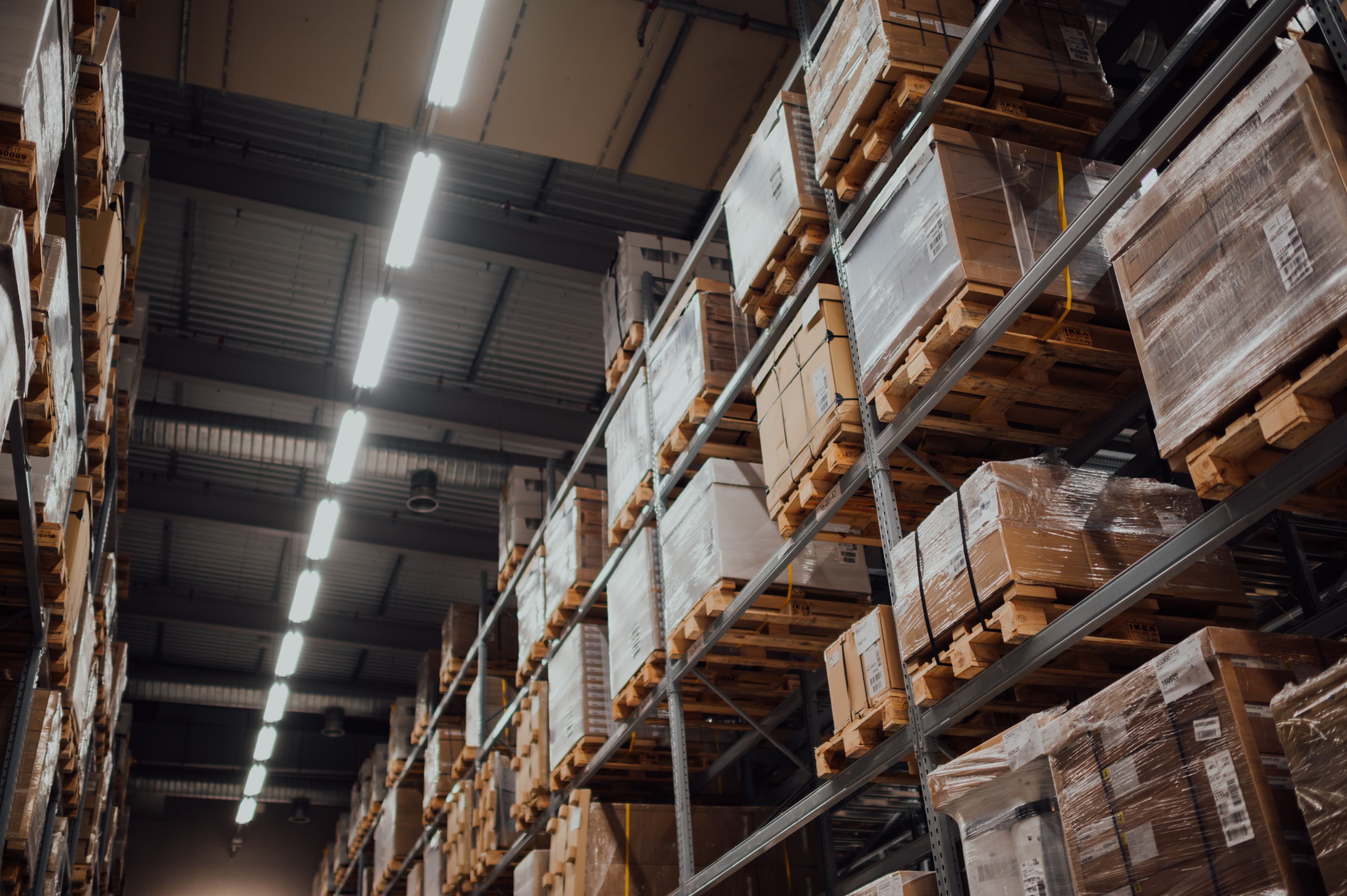
10 Proven Strategies for Improving Warehouse Productivity
The success of any warehouse operation relies heavily on its productivity. Efficient and well-managed warehouses can lead to increased profits and customer satisfaction, while poorly optimized warehouses can result in wasted time, resources, and money. In this article, we'll explore ten proven strategies for and maximizing your business's potential.
Understanding Warehouse Productivity
Before delving into specific strategies, it's important to first understand the importance of warehouse productivity. Warehouse productivity refers to the measure of how effectively resources, including time, space, and labor, are utilized to fulfill customer orders. A highly productive warehouse operates smoothly, minimizes waste, and consistently meets customer demands.
When it comes to warehouse productivity, there is more than meets the eye. It's not just about moving products from point A to point B; it's about optimizing every aspect of the warehouse operations to ensure maximum efficiency. From the layout and design of the warehouse to the use of technology and automation, every factor plays a crucial role in determining the overall productivity.
The Importance of Warehouse Productivity
Warehouse productivity directly impacts an organization's bottom line. When a warehouse operates efficiently, it leads to faster order fulfillment, reduced costs, and improved customer satisfaction. On the other hand, low warehouse productivity can result in delayed shipments, backorders, and dissatisfied customers. In today's fast-paced marketplace, optimizing warehouse productivity is crucial to staying competitive.
Imagine a scenario where a warehouse is disorganized, with products scattered randomly, and employees struggling to find what they need. This chaos not only slows down the order fulfillment process but also increases the chances of errors and damages. On the contrary, a well-organized warehouse, with clearly defined storage areas and efficient inventory management systems in place, can significantly improve productivity and minimize errors.
Key Factors Affecting Warehouse Productivity
Several key factors affect warehouse productivity. These include:
- Layout and design of the warehouse
- Efficient use of storage space
- Inventory management
- Effective use of technology and automation
- Employee training and motivation
Addressing these factors is integral to developing effective strategies for improving warehouse productivity. Let's take a closer look at each factor:
The layout and design of a warehouse play a critical role in optimizing productivity. A well-designed warehouse layout ensures smooth flow of goods, minimizes travel time, and reduces the risk of accidents. Factors such as the placement of aisles, storage racks, and workstations should be carefully considered to create an efficient workflow.
Storage space is a valuable resource in any warehouse. Maximizing the use of available space is essential to improve productivity. This can be achieved through the use of vertical storage solutions, such as high-rise racks and mezzanine floors, as well as implementing effective slotting techniques to optimize product placement.
Proper inventory management is crucial for warehouse productivity. Accurate tracking of stock levels, implementing efficient replenishment processes, and utilizing inventory management software can help prevent stockouts, reduce excess inventory, and improve overall efficiency.
Incorporating technology and automation into warehouse operations can greatly enhance productivity. This includes the use of barcode scanners, RFID systems, automated conveyor belts, and robotic picking systems. These technologies streamline processes, reduce manual errors, and increase throughput.
Investing in employee training and motivation is key to improving warehouse productivity. Well-trained employees are more efficient and make fewer mistakes. Providing ongoing training programs, incentives, and a positive work environment can boost employee morale and productivity.
Now that we have a better understanding of the factors influencing warehouse productivity, let's explore ten proven strategies to enhance warehouse productivity.
Strategy 1: Implementing Lean Warehouse Operations
Lean warehouse operations aim to eliminate waste and improve efficiency by focusing on continuous improvement and value-added activities. By implementing lean principles, warehouses can optimize workflows, reduce errors, and enhance productivity.
When it comes to , there are several key principles that organizations should keep in mind. These principles serve as a guide to help warehouses achieve their goals and create a culture of continuous improvement.
Principles of Lean Warehouse Operations
The principles of lean warehouse operations include:
- Identifying and eliminating waste: One of the fundamental principles of lean warehouse operations is the identification and elimination of waste. This can include unnecessary movement, excess inventory, and inefficient processes. By eliminating waste, warehouses can streamline their operations and maximize productivity.
- Streamlining processes: Another important principle is the streamlining of processes. This involves analyzing and optimizing workflows to reduce bottlenecks and improve overall efficiency. By streamlining processes, warehouses can minimize lead times and ensure that products are delivered to customers in a timely manner.
- Maintaining a clean and organized workspace: A clean and organized workspace is essential for lean warehouse operations. By keeping the warehouse clean and organized, employees can easily locate items, reduce errors, and improve overall productivity. Additionally, a clean and organized workspace promotes a safe working environment.
- Promoting employee involvement and empowerment: Employee involvement and empowerment are crucial for the success of lean warehouse operations. When employees are actively involved in the improvement process, they can provide valuable insights and suggestions for enhancing workflows. Empowering employees also fosters a sense of ownership and accountability, leading to increased engagement and productivity.
Benefits of Lean Warehouse Operations
Implementing lean warehouse operations offers several benefits, including:
- Reduced lead times: By eliminating waste and streamlining processes, lean warehouse operations can significantly reduce lead times. This means that products can be delivered to customers faster, resulting in improved customer satisfaction and increased competitiveness.
- Improved inventory accuracy: Lean warehouse operations prioritize accurate inventory management. By implementing strategies such as cycle counting and real-time tracking systems, warehouses can ensure that inventory levels are always up to date. This reduces the risk of stockouts or overstocking, leading to improved operational efficiency.
- Increased employee engagement: Lean warehouse operations promote employee involvement and empowerment, which in turn increases employee engagement. When employees feel valued and have a voice in the improvement process, they are more likely to be motivated and committed to their work. This can result in higher productivity and a positive work culture.
- Enhanced customer satisfaction: Ultimately, lean warehouse operations aim to enhance customer satisfaction. By reducing lead times, improving inventory accuracy, and increasing employee engagement, warehouses can meet customer demands more effectively. This leads to improved customer satisfaction, repeat business, and positive word-of-mouth recommendations.
Strategy 2: Utilizing Warehouse Management Systems
A robust warehouse management system (WMS) is essential for optimizing warehouse productivity. WMS software streamlines various warehouse processes, such as inventory management, order processing, and resource allocation.
Implementing a warehouse management system can revolutionize the way your warehouse operates. With its advanced features and capabilities, a WMS can help you achieve higher levels of efficiency and accuracy in your day-to-day operations.
One of the key features of an effective warehouse management system is real-time inventory tracking. With this feature, you can keep track of your inventory levels at all times, ensuring that you never run out of stock or overstock on certain items. This real-time visibility into your inventory can help you make informed decisions about reordering and replenishing stock, ultimately reducing the risk of stockouts and improving customer satisfaction.
Another important feature offered by warehouse management systems is order optimization and fulfillment. These systems can optimize the picking and packing process, ensuring that orders are fulfilled accurately and efficiently. By automating this process, you can minimize errors and reduce the time it takes to process orders, enabling you to meet customer demands faster and more effectively.
Integration with other business systems is another crucial feature of effective warehouse management systems. By integrating your WMS with other systems, such as your ERP or CRM, you can achieve seamless data flow and synchronization across your entire organization. This integration eliminates the need for manual data entry and reduces the risk of errors, allowing for more streamlined operations and improved overall efficiency.
Reporting and analytics capabilities are also essential in a warehouse management system. With these features, you can generate comprehensive reports and gain valuable insights into your warehouse operations. By analyzing data such as order volumes, picking times, and inventory turnover rates, you can identify areas for improvement and implement strategies to optimize your warehouse processes further.
Selecting the Right Warehouse Management System
When selecting a warehouse management system, there are several factors to consider. Scalability is one important factor to keep in mind. As your business grows, your warehouse needs may change, so it's crucial to choose a WMS that can scale with your operations. Look for a system that offers flexibility and can accommodate your future needs.
User-friendliness is another critical factor to consider. A WMS should be intuitive and easy to use, with a user-friendly interface that minimizes the learning curve for your warehouse staff. Training and onboarding should be straightforward, allowing your team to quickly adapt to the new system and start reaping its benefits.
Compatibility with your existing hardware and software is also essential. Ensure that the WMS you choose can seamlessly integrate with your current technology stack, including barcode scanners, mobile devices, and other equipment. This compatibility will prevent any disruptions to your operations and ensure a smooth transition to the new system.
Ultimately, selecting the right warehouse management system can significantly improve warehouse productivity and streamline operations. By leveraging the advanced features and capabilities of a WMS, you can optimize inventory management, enhance order processing, and achieve higher levels of efficiency and accuracy in your warehouse.
Strategy 3: Optimizing Warehouse Layout
The layout and design of a warehouse have a direct impact on its efficiency and productivity. By optimizing the warehouse layout, businesses can minimize travel time, reduce errors, and streamline processes.
When it comes to warehouse layout design, there are several principles that should be considered. These principles help create an optimized layout that maximizes space utilization and ensures smooth operations.
Principles of Warehouse Layout Design
When designing an optimized warehouse layout, consider the following principles:
- Utilize space efficiently: One of the key factors in warehouse layout optimization is making the most of available space. This involves carefully planning the placement of racks, shelves, and equipment to ensure optimal use of the warehouse's vertical and horizontal space.
- Organize products logically: A well-organized warehouse layout is essential for efficient inventory management. Grouping similar products together and arranging them in a logical order can significantly reduce picking and replenishment time.
- Minimize movement and travel distances: Another important principle is to minimize the distance traveled by warehouse staff and equipment. This can be achieved by strategically placing high-demand items closer to the shipping area and using efficient picking routes.
- Ensure clear pathways and safety measures: Safety should always be a top priority in warehouse layout design. Clear pathways should be established to prevent accidents and facilitate smooth movement of personnel and equipment. Safety measures such as proper lighting, signage, and designated areas for hazardous materials should also be implemented.
Tips for Warehouse Layout Optimization
To optimize warehouse layout, consider implementing techniques such as:
- Slotting optimization: Slotting optimization involves analyzing product demand and storage characteristics to determine the most efficient placement of items within the warehouse. By placing frequently picked items closer to the shipping area and organizing products based on their velocity, warehouse efficiency can be greatly improved.
- ABC analysis for inventory management: ABC analysis categorizes inventory based on its value and importance. By prioritizing high-value items and ensuring their accessibility, businesses can minimize picking time and improve overall efficiency.
- Implementing efficient picking strategies: Picking is a critical operation in any warehouse. By implementing efficient picking strategies such as batch picking or zone picking, businesses can reduce travel time and increase order fulfillment speed.
- Utilizing automation and technology: Automation and technology play a significant role in warehouse layout optimization. Automated systems such as conveyor belts, robotic picking systems, and inventory management software can greatly enhance efficiency and accuracy.
By following these principles and implementing optimization techniques, businesses can create a warehouse layout that maximizes efficiency, reduces costs, and improves overall productivity.
Strategy 4: Regular Employee Training
Investing in employee training is crucial for improving warehouse productivity. Well-trained employees are equipped with the skills and knowledge necessary to perform their tasks efficiently and effectively.
The Role of Training in Warehouse Productivity
Training plays a vital role in warehouse productivity by:
- Enhancing job skills and knowledge
- Improving safety awareness and compliance
- Promoting teamwork and collaboration
- Reducing errors and rework
Effective Training Techniques for Warehouse Staff
To ensure effective training for warehouse staff, consider the following techniques:
- Hands-on training sessions
- Product-specific training programs
- Mentorship and shadowing programs
- Regular refresher courses
Implementing these four strategies can yield significant improvements in warehouse productivity. However, there are additional strategies we'll explore in the second half of this article. Stay tuned to learn more about optimizing workforce scheduling, implementing cross-training programs, enhancing communication, leveraging data analytics, adopting automation technologies, and fostering a culture of continuous improvement.
Nitro Logistics Team
Logistics Expert
The Nitro Logistics team brings together decades of experience in logistics, fulfillment, and supply chain optimization.
Stay Updated
Get the latest insights in logistics and fulfillment delivered to your inbox.