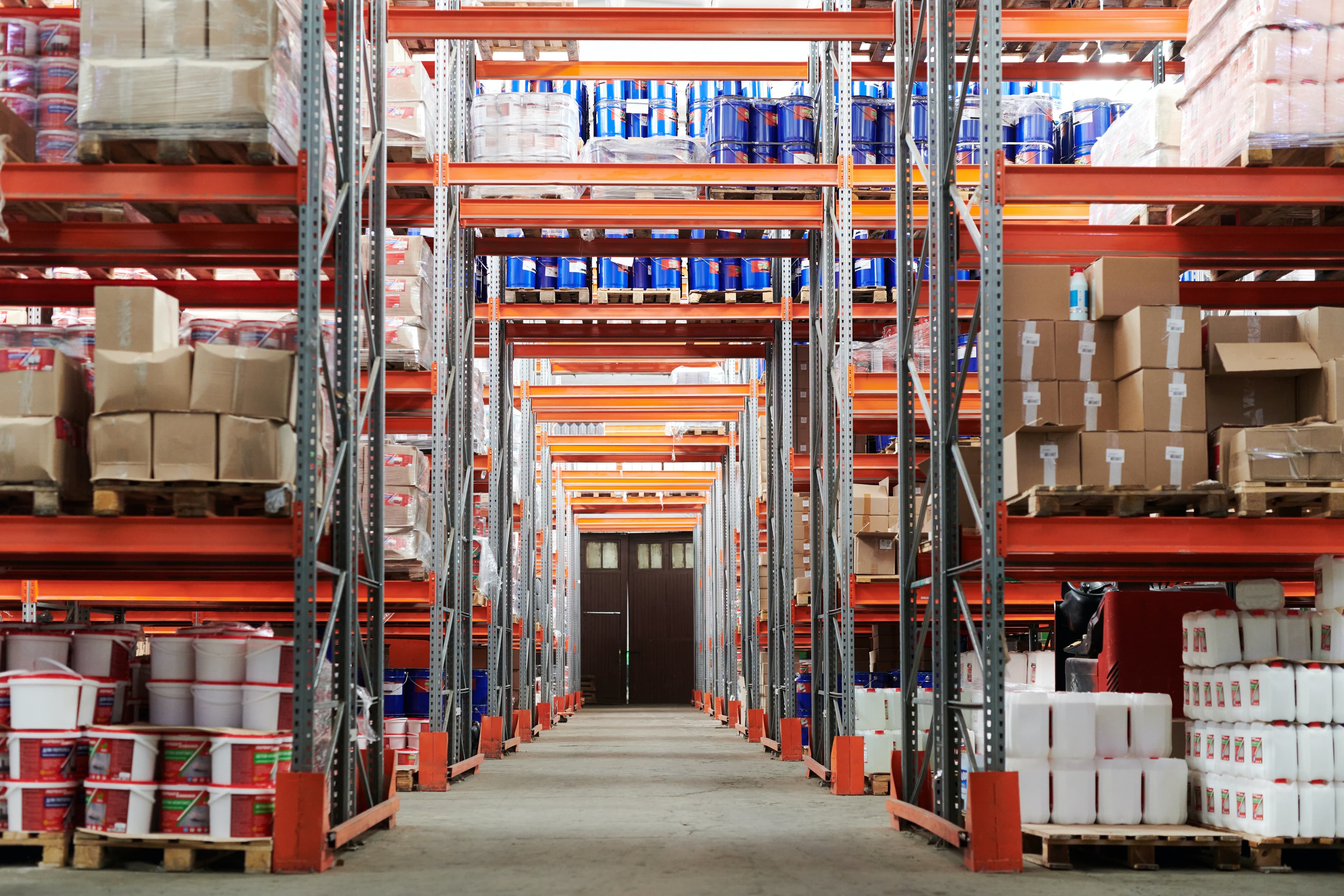
Continuous Improvement Strategies for Sustainable Warehouse Productivity
As the demands of the modern business landscape continue to evolve, warehouses face the ongoing challenge of meeting customers' expectations while maintaining high levels of productivity. One powerful approach that has emerged to address this challenge is continuous improvement. By embracing this concept and implementing effective strategies, warehouses can unlock their full potential and achieve sustainable productivity levels.
Understanding the Concept of Continuous Improvement
Continuous improvement is a philosophy and a mindset that emphasizes the importance of of doing things. It is based on the belief that even the most efficient processes can always be further optimized. In the context of warehousing, continuous improvement involves identifying opportunities to , reduce waste, and increase overall productivity.
When it comes to warehousing, the concept of continuous improvement is not just a buzzword; it is a critical aspect of staying competitive in today's fast-paced marketplace. Warehouses that embrace continuous improvement are able to reduce costs, enhance customer satisfaction, and stay ahead of the competition. By constantly seeking ways to improve processes, warehouses can adapt to changing customer demands and market trends.
One of the key benefits of continuous improvement in warehousing is the promotion of innovation. By encouraging employees to think critically about their work processes and identify areas for improvement, warehouses create an environment that fosters creativity and problem-solving. This, in turn, leads to the development of new and innovative solutions that can further enhance operational efficiencies.
The Importance of Continuous Improvement in Warehousing
Continuous improvement is vital for warehouses to remain competitive in today's fast-paced marketplace. By continuously seeking ways to improve processes, warehouses can reduce costs, enhance customer satisfaction, and stay ahead of the competition. Embracing a culture of continuous improvement also promotes innovation and empowers employees to take ownership of their work.
Furthermore, continuous improvement in warehousing helps to streamline operations and eliminate waste. By analyzing current processes and identifying areas for improvement, warehouses can , reduce errors, and optimize resource allocation. This not only improves overall productivity but also contributes to cost savings and improved profitability.
Another important aspect of continuous improvement in warehousing is the ability to adapt to changing customer needs and market trends. By constantly evaluating and improving processes, warehouses can ensure that they are able to meet customer demands in a timely and efficient manner. This agility and responsiveness are crucial in today's dynamic business environment, where customer expectations are constantly evolving.
Key Principles of Continuous Improvement
There are several key principles that underpin successful continuous improvement in warehousing:
- Customer Focus: Understanding and meeting the needs of customers drives improvement efforts. By actively seeking feedback from customers and aligning processes to meet their expectations, warehouses can continuously improve their operations to deliver superior value.
- Data-Driven Decision Making: Analyzing and using data to identify areas for improvement is a fundamental principle of continuous improvement. By collecting and analyzing data on key performance indicators, warehouses can gain insights into their operations and make informed decisions to drive improvements.
- Engaging Employees: Involving employees at all levels in the improvement process fosters a culture of continuous learning and innovation. By empowering employees to contribute their ideas and suggestions, warehouses can tap into their collective knowledge and experience to drive meaningful improvements.
- Standardization: Establishing standardized operating procedures to ensure consistency and efficiency is crucial for continuous improvement. By documenting and standardizing processes, warehouses can eliminate variations and inefficiencies, leading to improved productivity and quality.
By adhering to these key principles, warehouses can create a solid foundation for continuous improvement. It is important to note that continuous improvement is not a one-time effort but an ongoing journey. Warehouses must continuously evaluate their processes, monitor performance, and seek opportunities for further improvement to stay ahead in the competitive landscape.
Implementing Continuous Improvement Strategies in Warehousing
While the concept of continuous improvement may seem straightforward, implementing effective strategies requires careful planning and execution. Here are some steps to initiate continuous improvement in your warehouse:
Steps to Initiate Continuous Improvement
The first step is to clearly define the goals and objectives of continuous improvement for your warehouse. This could include reducing order processing times, improving inventory accuracy, or enhancing employee productivity. By setting specific and measurable goals, you can create a clear roadmap for improvement.
Once the goals are set, it is important to identify key performance indicators (KPIs) to measure progress and set targets for improvement. KPIs can include metrics such as order fulfillment rate, inventory turnover, and employee efficiency. These metrics will help you track your progress and identify areas that need improvement.
Next, establish a cross-functional improvement team consisting of representatives from different departments. This team will ensure a holistic approach to improvement efforts, as each department will bring unique perspectives and insights. By involving employees from various areas of the warehouse, you can tap into their expertise and leverage their knowledge to drive meaningful change.
Furthermore, it is crucial to encourage open communication and collaboration within the improvement team. This will foster a culture of continuous learning and innovation, where ideas can be shared and refined. By creating a supportive environment, team members will feel empowered to contribute their ideas and take ownership of the improvement process.
Overcoming Challenges in Implementation
Implementing continuous improvement strategies may encounter challenges along the way. Resistance to change, lack of resources, and a complacent culture are common obstacles that need to be addressed.
To overcome resistance to change, it is important to communicate the benefits of continuous improvement to all employees. Show them how it can lead to increased efficiency, reduced errors, and a better working environment. Provide training and support to help employees adapt to new processes and technologies, and address any concerns or fears they may have.
Lack of resources can also hinder the implementation of continuous improvement strategies. Ensure that you have the necessary tools, equipment, and technology to support your improvement efforts. This may involve investing in new software systems, upgrading machinery, or providing additional training to employees.
Another challenge is a complacent culture, where employees may resist change or become comfortable with the status quo. To overcome this, it is important to create a culture of continuous improvement. Recognize and celebrate small wins along the way, and acknowledge the contributions of employees who actively participate in improvement initiatives. This will help build momentum and sustain the improvement efforts over time.
In conclusion, implementing continuous improvement strategies in warehousing requires careful planning, clear goals, and a collaborative approach. By overcoming challenges and fostering a culture of continuous improvement, you can drive meaningful change and achieve long-term success in your warehouse operations.
Tools and Techniques for Continuous Improvement
Various tools and techniques can be utilized to support continuous improvement in warehousing:
Continuous improvement is a vital aspect of warehousing operations, as it allows businesses to enhance their efficiency, productivity, and overall performance. By implementing the right tools and techniques, warehouses can eliminate waste, streamline processes, and drive continuous improvement.
Lean Warehousing for Continuous Improvement
One of the most widely used methodologies for continuous improvement in warehousing is Lean. Derived from the Toyota Production System, Lean principles focus on eliminating waste and optimizing processes. By implementing Lean techniques, warehouses can achieve significant improvements in operational efficiency and productivity.
One of the key techniques used in Lean warehousing is 5S. This technique involves Sort, Set in Order, Shine, Standardize, and Sustain. By organizing the warehouse, eliminating clutter, and ensuring everything has a designated place, warehouses can reduce waste, improve workflow, and enhance overall efficiency.
Another valuable technique used in Lean warehousing is value stream mapping. This technique allows warehouses to visualize and analyze their current processes, identify areas of waste and inefficiency, and develop strategies for improvement. By mapping the value stream, warehouses can identify bottlenecks, reduce lead times, and enhance overall flow.
Kaizen events, another aspect of Lean warehousing, involve continuous improvement activities that focus on specific areas or processes within the warehouse. These events bring together cross-functional teams to identify opportunities for improvement, brainstorm solutions, and implement changes. By regularly conducting kaizen events, warehouses can foster a culture of continuous improvement and drive positive change.
Six Sigma in Warehouse Operations
Another powerful methodology for continuous improvement in warehousing is Six Sigma. Six Sigma provides a structured approach to identify and eliminate defects in processes, ultimately improving quality and reducing errors. By applying statistical analysis and problem-solving methodologies such as DMAIC (Define, Measure, Analyze, Improve, Control), warehouses can drive continuous improvement and achieve higher levels of performance.
The DMAIC process begins with defining the problem and setting clear goals for improvement. Warehouses then measure the current performance and collect data to analyze the root causes of defects or inefficiencies. Through careful analysis, warehouses can identify areas for improvement and develop strategies to address them.
After analyzing the data, warehouses move on to the improvement phase, where they implement changes and solutions to address the identified issues. This phase may involve process redesign, technology implementation, or training programs to enhance employee skills and knowledge.
Once the improvements are implemented, warehouses enter the control phase, where they establish monitoring systems to ensure the changes are sustained and continue to deliver the desired results. By continuously monitoring and measuring performance, warehouses can identify any deviations and take corrective actions to maintain the improvements achieved.
By incorporating Six Sigma methodologies into their operations, warehouses can drive continuous improvement, enhance quality, reduce errors, and ultimately achieve higher levels of customer satisfaction.
Measuring the Impact of Continuous Improvement
Measuring the impact of continuous improvement efforts is crucial to assess progress and identify areas for further enhancement. Key performance indicators (KPIs) play a critical role in this process:
When it comes to measuring warehouse productivity, there are several key performance indicators (KPIs) that can provide valuable insights. These metrics help warehouse managers gauge the effectiveness of their continuous improvement initiatives and identify areas for further optimization.
Key Performance Indicators for Warehouse Productivity
One important KPI is the order fulfillment rate. This metric measures the percentage of customer orders that are successfully fulfilled within a given time frame. A high order fulfillment rate indicates efficient order processing and timely delivery, while a low rate may indicate bottlenecks or inefficiencies in the warehouse operations.
Another KPI that is commonly used to measure warehouse productivity is inventory turnover. This metric calculates how quickly inventory is being sold and replenished. A high inventory turnover rate suggests that products are moving quickly, minimizing the risk of overstocking and reducing holding costs. On the other hand, a low turnover rate may indicate slow-moving inventory or poor demand forecasting.
Cycle time is another crucial KPI for measuring warehouse productivity. It refers to the time it takes for a product to move through the warehouse, from receiving to shipping. By tracking cycle time, warehouse managers can identify process bottlenecks and streamline operations to improve overall efficiency.
Picking accuracy is yet another important KPI for measuring warehouse productivity. This metric assesses the accuracy of order picking, ensuring that the correct items are selected and packed for shipment. High picking accuracy is crucial for customer satisfaction and minimizing returns or order errors.
These KPIs provide valuable insights into operational efficiency and can help track the effectiveness of continuous improvement initiatives. By regularly monitoring and analyzing these metrics, warehouse managers can identify areas for improvement and make data-driven decisions to optimize their operations.
Evaluating and Adjusting Improvement Strategies
Measuring the impact of continuous improvement efforts is not enough. It is essential to regularly evaluate and adjust improvement strategies based on data analysis and feedback. Continuous improvement should be an iterative process that embraces a culture of learning from both successes and failures.
By closely monitoring the results of improvement initiatives, warehouse managers can identify trends and patterns that indicate the effectiveness of their strategies. They can then make necessary adjustments to further enhance productivity and operational efficiency.
Feedback from employees and customers also plays a crucial role in evaluating improvement strategies. Warehouse managers should actively seek input from their team members to gain insights into potential areas for improvement. Additionally, gathering feedback from customers can provide valuable information on their satisfaction levels and identify any pain points in the order fulfillment process.
Continuous improvement is an ongoing journey, and it requires a proactive approach to stay on track. By regularly evaluating and adjusting improvement strategies, warehouses can ensure that their efforts remain aligned with organizational goals and drive sustainable growth.
Maintaining Sustainable Warehouse Productivity
While implementing continuous improvement strategies is vital, it is equally important to maintain sustainable productivity levels over the long term. Here are some factors to consider:
Role of Employee Engagement in Sustaining Productivity
Engaged employees are more likely to be motivated, innovative, and committed to continuous improvement. Creating a positive work environment that values employee input, recognizes achievements, and fosters a culture of collaboration and growth is essential for sustaining productivity gains.
The Future of Sustainable Warehouse Productivity
The landscape of warehousing continues to evolve, with emerging technologies such as automation, artificial intelligence, and robotics playing an increasingly significant role. To remain competitive and sustain productivity in the future, warehouses must embrace these technological advancements, adapt to changing customer demands, and continue to foster a culture of continuous improvement.
In conclusion, continuous improvement strategies are essential for warehouses to achieve sustainable productivity levels. By understanding the concept of continuous improvement, implementing effective strategies, leveraging appropriate tools and techniques, measuring impact, and maintaining employee engagement, warehouses can unlock their full potential and thrive in a rapidly changing business environment. Embracing a culture of continuous improvement is not only a strategic decision but a powerful mindset that drives innovation, efficiency, and competitive advantage.
Nitro Logistics Team
Logistics Expert
The Nitro Logistics team brings together decades of experience in logistics, fulfillment, and supply chain optimization.
Stay Updated
Get the latest insights in logistics and fulfillment delivered to your inbox.