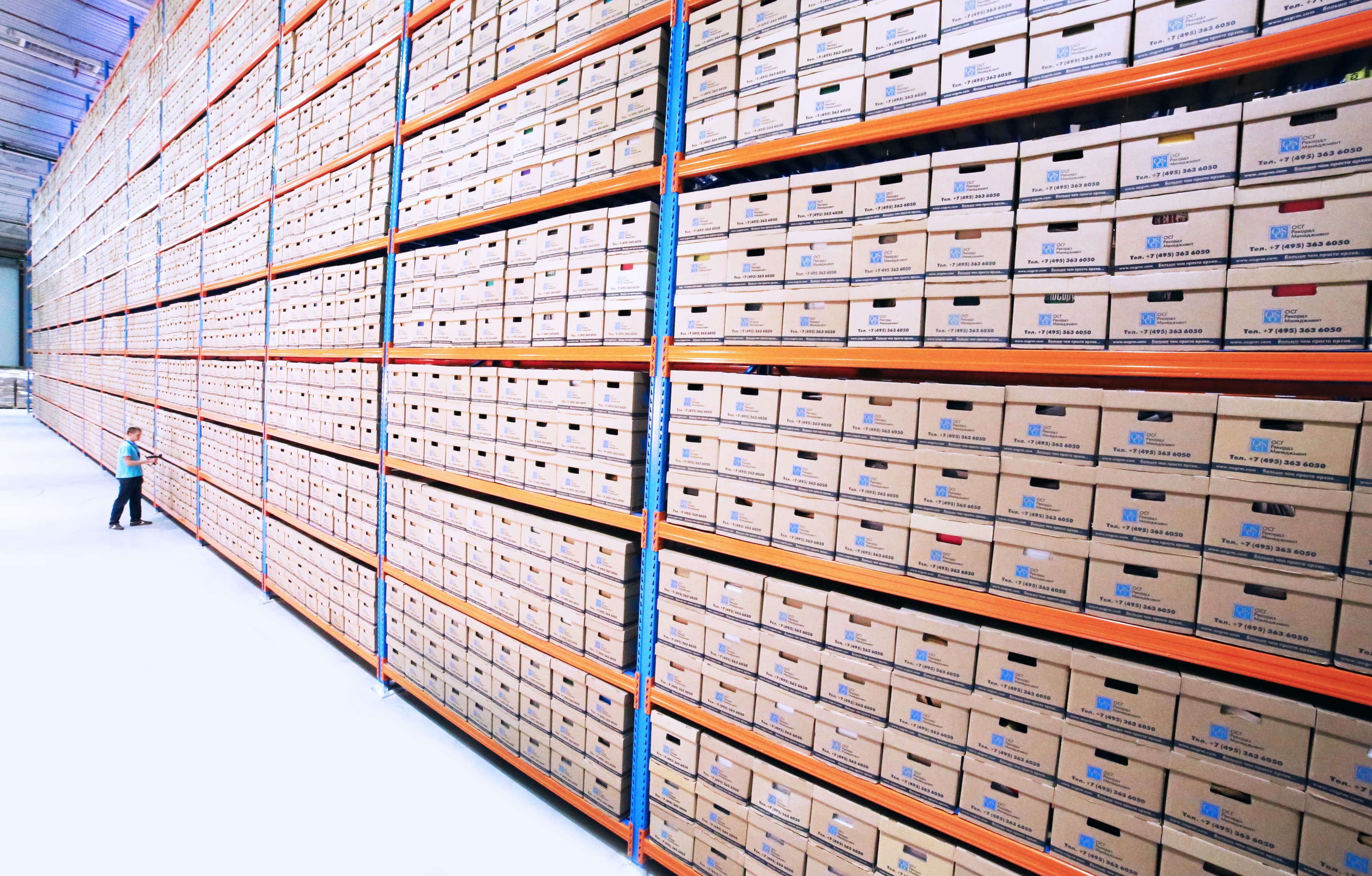
Implementing Lean Principles in Warehouse Operations
In today's fast-paced business environment, optimizing warehouse operations is essential to stay competitive. One approach that has gained significant attention and proved to be highly effective is implementing Lean Principles. By embracing this philosophy, warehouses can enhance efficiency, reduce waste, and maximize value. In this article, we will explore the various aspects of Lean Principles and provide a comprehensive guide on how to implement them in warehouse operations.
Understanding Lean Principles
Before diving into the implementation process, it is vital to understand the philosophy behind Lean Principles. At its core, Lean is about relentlessly pursuing perfection through the elimination of waste. By focusing on value-adding activities and continuous improvement, Lean Principles drive operational excellence and long-term success.
The Philosophy Behind Lean Principles
The philosophy behind Lean Principles revolves around creating a culture of continuous improvement, where waste is systematically identified and eliminated. It encourages a shift in mindset, empowering employees to proactively identify opportunities for improvement and take ownership of the process.
When implementing Lean Principles, organizations often adopt a set of core values that guide their actions. These values include respect for people, a focus on teamwork, and a commitment to delivering value to customers. By embodying these values, organizations create an environment that fosters collaboration, innovation, and a relentless pursuit of excellence.
One of the fundamental concepts in Lean is the concept of waste. Waste refers to any activity or process that does not add value to the customer. Lean Principles encourage organizations to identify and eliminate different types of waste, such as overproduction, defects, waiting, unnecessary transportation, excess inventory, unnecessary motion, and underutilized talent. By reducing or eliminating waste, organizations can improve efficiency, reduce costs, and enhance customer satisfaction.
Key Components of Lean Principles
Several key components make up Lean Principles, including:
- Value: Value refers to any activity that directly contributes to meeting customer needs and expectations. It is essential to understand what customers perceive as valuable to ensure that resources are allocated effectively.
- Value Stream: The value stream represents the entire process involved in delivering a product or service, from raw materials to the end consumer. It includes all the steps, activities, and resources required to transform inputs into outputs. Understanding the value stream is crucial for identifying waste and opportunities for improvement.
- Flow: Flow focuses on eliminating bottlenecks and disruptions to ensure a smooth and continuous process flow. It involves optimizing the sequence of activities, reducing cycle times, and minimizing interruptions. By achieving a steady flow, organizations can improve productivity and responsiveness.
- Pull: Pull refers to the practice of producing based on customer demand rather than pushing goods into the system, reducing inventory and waste. By adopting a pull system, organizations can avoid overproduction, reduce lead times, and improve customer satisfaction. Pull systems rely on real-time information, close collaboration with suppliers, and flexible production processes.
- Continuous Improvement: This component emphasizes the constant pursuit of perfection through incremental and iterative improvements. Organizations that embrace continuous improvement encourage employees at all levels to identify and implement small changes that lead to significant results over time. This philosophy promotes a culture of learning, experimentation, and adaptation.
Implementing Lean Principles requires a holistic approach that considers the entire value chain, from suppliers to customers. It involves engaging employees, fostering a culture of collaboration and innovation, and to drive decision-making. By embracing Lean Principles, organizations can achieve operational excellence, enhance customer satisfaction, and gain a competitive advantage in today's dynamic business environment.
The Importance of Lean Principles in Warehousing
Implementing Lean Principles in warehouse operations offers numerous benefits that significantly impact productivity and overall business performance.
Warehousing is a critical component of the supply chain, serving as a hub for storing, organizing, and distributing goods. Efficient warehouse operations are essential for businesses to meet customer demands, reduce costs, and stay competitive in the market.
Lean Principles streamline processes, remove unnecessary steps, and optimize resource utilization, resulting in increased efficiency and productivity. By eliminating waste, such as excess inventory, non-value-adding activities, and transportation inefficiencies, warehouses can reduce lead times and improve customer satisfaction.
One of the key aspects of Lean Principles is the concept of continuous improvement. Warehouse managers and employees are encouraged to identify areas for improvement and implement changes to enhance operations. This culture of continuous improvement fosters innovation, problem-solving, and collaboration within the warehouse environment.
Enhancing Efficiency and Productivity
Lean Principles play a crucial role in enhancing efficiency and productivity in warehouse operations. By implementing practices such as 5S (Sort, Set in Order, Shine, Standardize, Sustain), warehouses can create a clean and organized work environment. This allows employees to locate items quickly, reduce errors, and minimize wasted time searching for misplaced goods.
Furthermore, Lean Principles emphasize the importance of . This ensures that tasks are performed consistently and reduces the likelihood of errors or rework. By standardizing processes, warehouses can achieve higher levels of efficiency and productivity.
Another aspect of Lean Principles is the implementation of visual management techniques. Visual cues, such as color-coded labels, floor markings, and signage, help employees easily identify and locate items, reducing the time spent searching for products. Visual management also promotes safety by highlighting potential hazards and reminding employees of safety protocols.
Reducing Waste and Maximizing Value
Waste is a significant concern in warehouse operations, as it consumes resources and hinders competitiveness. Lean Principles focus on eliminating waste in all its forms, including inventory excess, overproduction, waiting times, transportation inefficiencies, and defects.
By implementing Just-in-Time (JIT) inventory management, warehouses can reduce the amount of inventory held, minimizing storage costs and the risk of obsolescence. JIT ensures that inventory is replenished only when needed, reducing the need for large stockpiles and freeing up valuable warehouse space.
Lean Principles also emphasize the importance of error-proofing processes to minimize defects and rework. By implementing quality control measures, such as visual inspections, error-proofing devices, and employee training, warehouses can reduce the occurrence of defects and improve overall product quality.
Furthermore, Lean Principles encourage the use of cross-functional teams and collaboration among different departments within the warehouse. This promotes knowledge sharing, problem-solving, and the identification of improvement opportunities. By involving employees from various areas of expertise, warehouses can leverage their collective knowledge and experience to drive continuous improvement and maximize value.
In conclusion, implementing Lean Principles in warehouse operations is crucial for enhancing efficiency, reducing waste, and maximizing value. By streamlining processes, eliminating waste, and fostering a culture of continuous improvement, warehouses can achieve higher levels of productivity, improve customer satisfaction, and gain a competitive edge in the market.
Steps to Implement Lean Principles in Warehouse Operations
Implementing Lean Principles requires a structured approach. By following these steps, warehouses can successfully integrate Lean into their operations.
Identifying Value in Warehouse Processes
The first step in implementing Lean Principles is identifying value from the customer's perspective. By understanding what activities and processes contribute directly to customer satisfaction, warehouses can prioritize their efforts and eliminate wasteful practices.
For example, warehouses can conduct customer surveys or analyze customer feedback to gain insights into their preferences and expectations. By understanding the value that customers place on certain processes, warehouses can focus their resources on improving those areas and eliminating any activities that do not contribute to customer satisfaction.
Mapping the Value Stream
Once the value-adding activities are identified, the next step is mapping the value stream. This involves visualizing the entire flow of materials, information, and processes within the warehouse. By identifying bottlenecks and areas of waste, warehouses can develop strategies for improvement.
During the mapping process, warehouses can use tools such as process flow diagrams, value stream maps, and spaghetti diagrams to identify the flow of materials and information throughout the warehouse. This detailed visualization helps warehouse managers and employees understand the current state of operations and identify areas for improvement.
Creating Flow and Establishing Pull
Creating flow involves designing processes that allow for efficient and uninterrupted movement. By eliminating obstacles and improving material flow, warehouses can reduce waiting times and optimize resource utilization. Establishing a pull system ensures that production and replenishment are triggered by actual customer demand, minimizing excess inventory and waste.
To create flow, warehouses can implement strategies such as rearranging the layout of the warehouse to minimize travel distances, implementing standardized work procedures to ensure consistent processes, and using visual management tools to improve communication and coordination among employees.
Establishing a pull system involves setting up processes that respond to customer demand. This can be achieved through techniques such as just-in-time inventory management, where materials are replenished only when needed, and kanban systems, which use visual signals to trigger production or replenishment.
Pursuing Perfection through Continuous Improvement
The final step in implementing Lean Principles is pursuing perfection through continuous improvement. Warehouse operations should establish a culture of ongoing evaluation, setting performance targets, and empowering employees to suggest and implement improvements. By embracing a mindset of continuous learning and adaptation, warehouses can stay ahead of the competition.
Continuous improvement can be achieved through various methods, such as conducting regular performance reviews, implementing employee suggestion programs, and fostering a culture of innovation and experimentation. By encouraging employees to actively participate in improving warehouse processes, warehouses can tap into their collective knowledge and experience to drive continuous improvement.
Furthermore, warehouses can also benchmark their performance against industry best practices and seek external expertise through partnerships or consulting services to gain fresh insights and ideas for improvement.
Challenges in Implementing Lean Principles
While Lean Principles offer substantial benefits, implementing them in warehouse operations may present some challenges.
One of the major challenges in implementing Lean Principles is overcoming resistance to change. Implementing Lean Principles often requires a cultural shift within the organization. Resistance to change from employees and management can hinder progress and make it difficult to achieve the desired improvements. Overcoming this challenge entails effective communication, training programs, and creating a supportive environment that encourages innovation and continuous improvement.
Another challenge in implementing Lean Principles is ensuring adequate training and skill development. Lean Principles rely heavily on employee involvement and empowerment. To optimize the implementation process, warehouses should invest in training programs that equip employees with the necessary skills and knowledge to participate effectively in Lean initiatives. Providing comprehensive training not only helps employees understand the principles and techniques but also enables them to contribute to the continuous improvement efforts.
In addition to resistance to change and training challenges, another obstacle in implementing Lean Principles is the need for effective leadership. Lean initiatives require strong leadership to drive the change and ensure its sustainability. Leaders need to set clear goals, communicate the vision, and provide the necessary support and resources to implement Lean Principles successfully. They also need to foster a culture of accountability and continuous improvement, encouraging employees to take ownership of their work and actively contribute to Lean initiatives.
Furthermore, implementing Lean Principles may also require significant investment in technology and infrastructure. Lean Principles often rely on advanced technologies, such as automation and data analytics, to optimize processes and improve efficiency. Warehouses may need to invest in new equipment, software, and systems to support Lean implementation. Additionally, they may need to redesign their layout and workflow to eliminate waste and create a more streamlined operation.
Lastly, sustaining the gains achieved through Lean implementation can be a challenge. Continuous improvement is a fundamental aspect of Lean Principles, and organizations need to ensure that the improvements made are sustained over time. This requires ongoing monitoring, measurement, and feedback mechanisms to identify any deviations from the desired state and take corrective actions promptly. It also requires a commitment to a culture of continuous improvement, where employees are encouraged to identify and address issues proactively.
Measuring the Success of Lean Implementation
In order to track progress and ensure the effectiveness of Lean implementation, warehouses should establish key performance indicators (KPIs) specific to Lean principles in warehousing.
Key Performance Indicators for Lean Warehousing
Some key performance indicators that can be used to measure the success of Lean implementation in warehousing include:
- Inventory turnover: The rate at which inventory is sold and replaced, indicating how efficiently goods flow through the warehouse.
- Lead time: The time it takes to fulfill customer orders, reflecting the efficiency of the order fulfillment process.
- Defect rate: The percentage of defective products or errors in the warehouse processes, indicating the effectiveness of quality control measures.
- On-time delivery: The percentage of orders delivered within the promised timeframe, reflecting customer satisfaction and order fulfillment efficiency.
Continuous Monitoring and Improvement
Measuring success is not enough; continuous monitoring and improvement are crucial components of Lean Principles. By regularly reviewing KPIs, warehouses can identify areas for further optimization and take corrective actions to sustain long-term success.
In conclusion, implementing Lean Principles in warehouse operations can revolutionize the way warehouses operate. By embracing Lean Philosophy, understanding its key components, and following a structured implementation process, warehouses can unlock significant cost savings, improve efficiency, and maximize customer value. Although challenges may arise, overcoming them through effective change management and continuous improvement will ensure long-term success in warehouse operations.
Nitro Logistics Team
Logistics Expert
The Nitro Logistics team brings together decades of experience in logistics, fulfillment, and supply chain optimization.
Stay Updated
Get the latest insights in logistics and fulfillment delivered to your inbox.