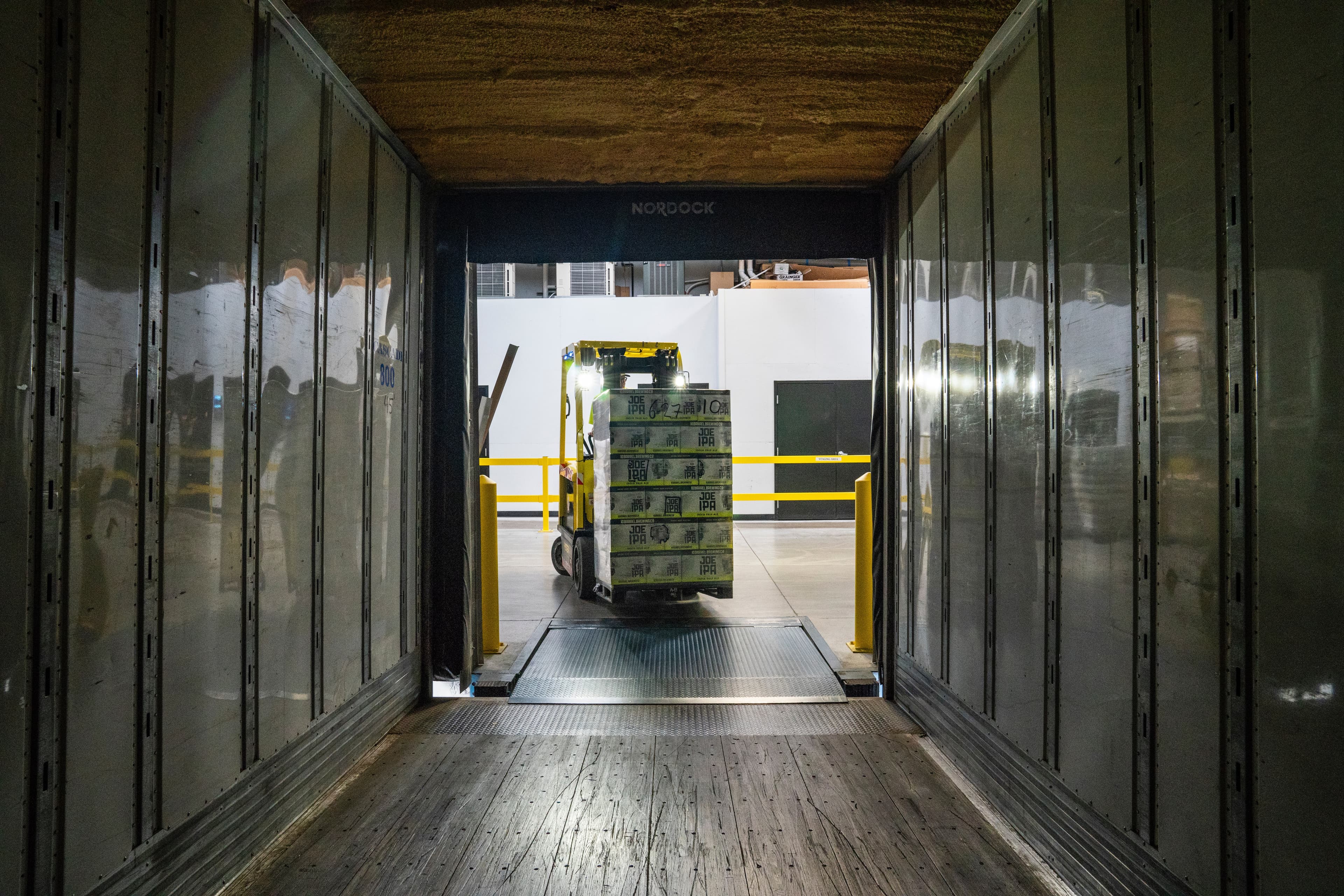
Streamlining Warehouse Operations: Best Practices for Improved Productivity
In today's fast-paced business landscape, streamlining warehouse operations is essential for companies looking to achieve improved productivity and stay competitive. A seamlessly functioning warehouse not only ensures but also contributes to overall customer satisfaction. In this article, we will explore the key elements of warehouse operations and delve into best practices that can be implemented to optimize productivity.
Understanding the Basics of Warehouse Operations
Before we dive into streamlining techniques, it's important to understand the role of warehousing in supply chain management and the key components that make up warehouse operations.
Warehousing plays a crucial role in the supply chain by acting as a central hub for inventory storage and distribution. It serves as a buffer between production and the end customer, allowing for better demand management and order fulfillment.
When it comes to supply chain management, warehousing is not just about storing products. It involves a complex set of processes and activities that ensure the smooth flow of goods from the point of origin to the point of consumption.
One of the key components of warehouse operations is receiving and inspecting incoming shipments. This involves carefully checking the quantity and quality of the products received, verifying them against the purchase orders, and documenting any discrepancies. It is crucial to have a robust system in place to accurately track and manage incoming inventory.
Another important aspect of warehouse operations is inventory storage. Efficient utilization of warehouse space is essential to maximize storage capacity and minimize costs. This includes organizing products in a logical and systematic manner, implementing proper labeling and identification systems, and regularly conducting stock audits to ensure .
Order picking and packing is another critical function of warehouse operations. This involves retrieving the correct items from the storage location, assembling them into customer orders, and preparing them for shipment. Efficient order picking strategies, such as batch picking or zone picking, can significantly improve productivity and reduce order fulfillment time.
Once the orders are picked and packed, the final component of warehouse operations is shipping. This involves coordinating with logistics providers, arranging transportation, and ensuring timely delivery to the customers. Proper documentation and labeling of shipments are essential to avoid any delays or errors in the delivery process.
Ensuring seamless coordination and efficient execution of these tasks is vital to optimizing overall warehouse performance. This requires effective communication and collaboration among different departments within the warehouse, as well as with external stakeholders such as suppliers, customers, and transportation providers.
In conclusion, warehouse operations are a critical part of supply chain management. Understanding the role of warehousing and the key components involved can help businesses streamline their operations and improve overall efficiency.
The Need for Streamlining Warehouse Operations
Traditional warehouse management methods often face various challenges that hinder productivity and create bottlenecks within the supply chain. Understanding the need for streamlining operations is the first step towards achieving a more efficient and productive warehouse environment.
When it comes to traditional warehouse management, there are several challenges that organizations commonly encounter. These challenges can have a significant impact on the overall efficiency and effectiveness of warehouse operations.
Challenges in Traditional Warehouse Management
One of the main challenges is the reliance on outdated manual processes. In a traditional warehouse, tasks such as inventory tracking, order processing, and resource allocation are often done manually, leading to inefficiencies and errors. This manual approach not only consumes valuable time but also increases the likelihood of mistakes, resulting in delays and additional costs.
Another challenge is the inefficient layout design of the warehouse. In many traditional warehouses, the layout is not optimized for maximum efficiency. This can lead to unnecessary travel time for workers, as they have to navigate through a maze of aisles and shelves to locate and retrieve items. Inefficient layout designs also make it difficult to implement effective inventory management strategies, further impacting productivity.
Lack of real-time inventory visibility is yet another challenge faced in traditional warehouse management. Without accurate and up-to-date information on inventory levels, it becomes challenging to make informed decisions regarding order fulfillment, stock replenishment, and overall resource allocation. This lack of visibility can result in overstocking or stockouts, both of which have negative consequences for warehouse operations.
Suboptimal resource allocation is also a common challenge. In traditional warehouses, resources such as labor, equipment, and storage space are often not allocated optimally. This can lead to underutilization of resources, inefficient workflows, and increased costs. Without proper resource allocation, warehouses struggle to meet customer demands in a timely and cost-effective manner.
The Impact of Inefficient Warehouse Operations
The consequences of inefficient warehouse operations extend beyond the internal workings of the warehouse. In fact, the impact can be felt by customers and partners as well.
One of the significant impacts is inaccurate inventory counts. When warehouse operations are not streamlined, inventory counts can be prone to errors. This can result in discrepancies between the actual stock levels and what is recorded in the system. Inaccurate inventory counts can lead to stockouts, where customers are unable to purchase the products they desire, or overstocking, which ties up valuable capital and storage space.
Delayed order fulfillment is another consequence of inefficient warehouse operations. When manual processes, inefficient layout designs, and suboptimal resource allocation are present, it takes longer to process and fulfill customer orders. This delay can lead to dissatisfied customers who may choose to take their business elsewhere, impacting the reputation and profitability of the organization.
Inadequate tracking is yet another impact of inefficient warehouse operations. Without real-time visibility into the movement of goods within the warehouse, it becomes difficult to track the progress of orders and provide accurate delivery estimates to customers. This lack of tracking can result in missed delivery deadlines, further frustrating customers and damaging the organization's reputation.
Additionally, inefficient warehouse operations can strain partnerships with suppliers and distributors. When orders are delayed, inventory is inaccurately managed, and tracking is inadequate, it can lead to strained relationships with business partners. This can result in missed business opportunities, as partners may choose to work with more efficient and reliable organizations.
In conclusion, the challenges faced in traditional warehouse management and the impact of inefficient operations highlight the need for streamlining warehouse processes. By implementing modern technologies, optimizing layout designs, improving inventory visibility, and allocating resources effectively, organizations can enhance productivity, reduce costs, and improve customer satisfaction.
Best Practices for Streamlining Warehouse Operations
Implementing a set of best practices can transform a warehouse from a cost center to a strategic asset. Let's explore some proven techniques that can help streamline warehouse operations and enhance overall productivity.
Efficient warehouse operations are crucial for businesses to meet customer demands and stay competitive in today's fast-paced market. By implementing the right strategies and utilizing advanced technologies, warehouses can , reduce costs, and improve customer satisfaction.
Implementing Warehouse Management Systems
A Warehouse Management System (WMS) is a software solution that provides real-time visibility, automates inventory tracking, streamlines order processing, and optimizes resource allocation. By implementing a WMS, warehouses can significantly enhance operational efficiency and reduce errors.
With a WMS in place, warehouse managers can have complete visibility into their inventory levels, ensuring accurate stock counts and preventing stockouts or overstock situations. The system can also automate order fulfillment processes, reducing the time and effort required for manual order processing. By optimizing resource allocation, warehouses can minimize labor costs and improve overall productivity.
Adopting Lean Warehousing Principles
Lean warehousing aims to eliminate waste and maximize value-add activities. By implementing lean principles such as Kaizen, 5S methodology, and just-in-time inventory management, warehouses can reduce downtime, inventory holding costs, and improve overall workflow efficiency.
Kaizen, a Japanese term meaning continuous improvement, encourages warehouse staff to identify and eliminate inefficiencies in their processes. By regularly reviewing and refining workflows, warehouses can continuously optimize their operations and achieve higher levels of productivity.
The 5S methodology, which stands for Sort, Set in Order, Shine, Standardize, and Sustain, helps warehouses organize their workspaces and maintain cleanliness. By implementing this methodology, warehouses can reduce time wasted searching for items, improve safety, and create a more efficient and visually appealing environment.
Just-in-time inventory management is another important aspect of lean warehousing. By closely monitoring customer demand and adjusting inventory levels accordingly, warehouses can minimize excess inventory and reduce carrying costs.
Enhancing Warehouse Layout and Design
An optimized warehouse layout ensures efficient material flow, minimizes travel distances, and maximizes space utilization. By analyzing product velocity, conducting slotting analysis, and implementing proper zoning, warehouses can improve picking efficiency and reduce congestion.
Product velocity analysis involves categorizing products based on their demand patterns and placing high-demand items closer to the shipping area. This reduces the time and effort required for order picking and improves order fulfillment speed.
Slotting analysis helps determine the most efficient locations for storing products within the warehouse. By considering factors such as product dimensions, weight, and demand, warehouses can optimize their storage space and minimize unnecessary movement of goods.
Proper zoning involves dividing the warehouse into different areas based on the type of products or their storage requirements. This ensures that similar products are stored together, reducing the time required for order picking and minimizing the risk of errors.
Additionally, warehouses can leverage technology such as barcode scanning and automated guided vehicles (AGVs) to further enhance their operational efficiency. Barcode scanning enables accurate and efficient inventory tracking, while AGVs can automate material handling tasks, reducing the reliance on manual labor and improving overall productivity.
The Role of Technology in Warehouse Streamlining
Technology plays an increasingly important role in streamlining warehouse operations. With the constant evolution of technology, warehouses have been able to optimize their processes and improve efficiency. Two key areas where technological advancements have made a significant impact are automation and the Internet of Things (IoT).
The Rise of Automation and Robotics in Warehousing
Automation technologies have revolutionized the way warehouses operate. One of the most notable advancements is the implementation of autonomous guided vehicles (AGVs). These robotic vehicles are equipped with sensors and software that allow them to navigate through the warehouse autonomously, picking up and delivering items. AGVs have significantly enhanced order picking efficiency, reducing the time it takes to fulfill orders and improving overall productivity.
In addition to AGVs, robotic picking systems have also become increasingly popular in warehouses. These systems use advanced algorithms and robotic arms to pick and pack items with precision and speed. By automating the picking process, warehouses can reduce labor costs and improve accuracy, as robots are less prone to errors compared to human workers.
Conveyor systems have also played a crucial role in warehouse automation. These systems use a network of belts, rollers, and sensors to transport items throughout the warehouse. By eliminating the need for manual transportation, conveyor systems streamline the flow of goods, reducing the time it takes to move items from one location to another.
The Impact of IoT on Warehouse Efficiency
The Internet of Things (IoT) has brought about a new era of connectivity and data-driven decision making in warehouses. IoT technology enables real-time inventory tracking, predictive maintenance, and advanced analytics for better decision making.
By leveraging IoT sensors, warehouses can gain visibility into inventory levels in real-time. These sensors can be attached to shelves, pallets, or individual items, allowing warehouse managers to monitor stock levels accurately. With this information, warehouses can optimize their inventory management, ensuring that they have the right amount of stock at all times, avoiding stockouts or overstocking.
Predictive maintenance is another area where IoT has made a significant impact. By equipping equipment and machinery with IoT sensors, warehouses can monitor their condition in real-time. These sensors can detect anomalies, such as unusual vibrations or temperature changes, and alert maintenance teams before a breakdown occurs. By proactively addressing maintenance issues, warehouses can minimize downtime and ensure that their operations run smoothly.
Furthermore, IoT enables advanced analytics, allowing warehouses to analyze vast amounts of data to make informed decisions. By collecting data from various sources, such as inventory levels, order volumes, and customer demand, warehouses can identify patterns and trends. This information can be used to optimize order fulfillment processes, streamline operations, and improve overall efficiency.
In conclusion, technology, particularly automation and IoT, has revolutionized warehouse operations. From autonomous guided vehicles to IoT sensors, these advancements have significantly improved efficiency, reduced labor costs, and enhanced decision-making capabilities. As technology continues to evolve, warehouses can expect further advancements that will continue to streamline their operations and drive greater success.
Measuring the Success of Streamlined Warehouse Operations
Continuous improvement is vital for maintaining a successful warehouse operation. Key Performance Indicators (KPIs) help assess the effectiveness of optimization efforts and highlight areas for further improvement.
Key Performance Indicators for Warehouse Operations
Common KPIs for warehouse operations include order accuracy, on-time delivery, order cycle time, inventory turnover, and picking accuracy. Regularly monitoring these metrics and benchmarking against industry standards can identify performance gaps and drive continuous improvement initiatives.
Continuous Improvement in Warehouse Management
Streamlining warehouse operations is an ongoing process. By fostering a culture of continuous improvement, encouraging employee feedback, and regularly reviewing processes, warehouses can adapt to changing market dynamics and consistently optimize productivity.
Conclusion
Streamlining warehouse operations requires a multi-faceted approach that encompasses process optimization, technology adoption, and continuous improvement. By implementing best practices, leveraging technology, and focusing on efficiency, warehouses can unlock untapped potential, reduce costs, and ultimately improve customer satisfaction. Embracing these strategies will position warehouses at the forefront of the ever-evolving supply chain landscape.
Nitro Logistics Team
Logistics Expert
The Nitro Logistics team brings together decades of experience in logistics, fulfillment, and supply chain optimization.
Stay Updated
Get the latest insights in logistics and fulfillment delivered to your inbox.