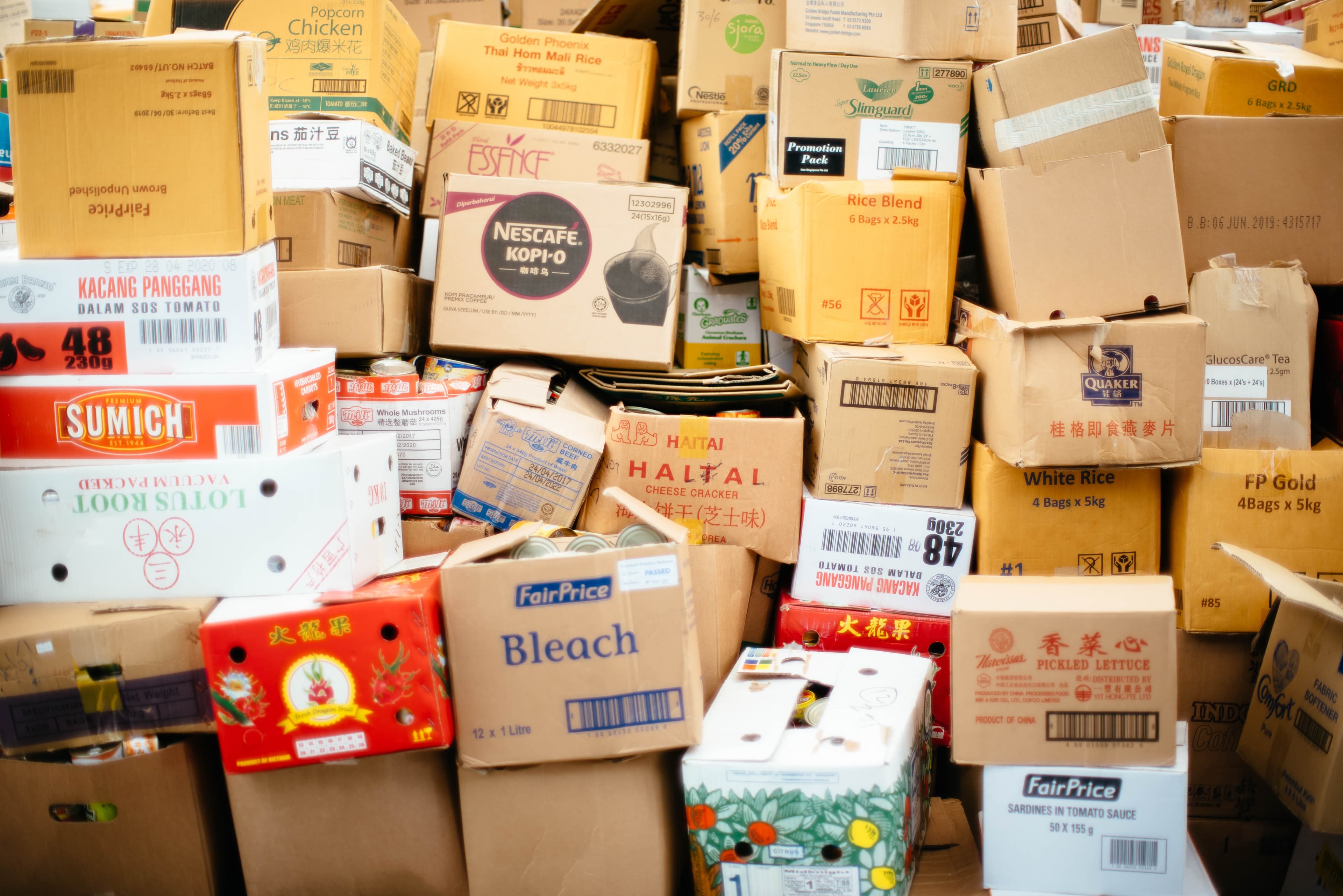
Supply Chain Bottlenecks: Causes, Challenges & How to Navigate Them
Supply chains are an essential part of any business operation. They ensure that goods move seamlessly from production to distribution to the hands of customers. However, in today's complex global economy, supply chain bottlenecks are a common challenge that businesses face. These bottlenecks can cause delays, inefficiencies, and frustrations for both businesses and customers. In this article, we will explore the causes of supply chain bottlenecks, the challenges they pose, and strategies to navigate them effectively.
Understanding Supply Chain Bottlenecks
Before delving into the causes and challenges, let's first define what supply chain bottlenecks are. Simply put, a bottleneck in the supply chain refers to any point in the process where the flow of goods is hindered or constrained. This can arise from various factors such as production issues, transportation delays, or demand fluctuations. Regardless of the specific cause, the result is a disruption to the smooth flow of goods through the supply chain.
Defining Supply Chain Bottlenecks
A supply chain bottleneck can occur at any stage of the process, from the procurement of raw materials to the final delivery of finished products. It is essentially a point where the capacity of a particular process or resource is exceeded, causing a slowdown or halt in operations. These bottlenecks can have a cascading effect, impacting subsequent stages of the supply chain and eventually causing delays and inefficiencies throughout the entire system.
For example, let's consider a manufacturing company that produces electronic devices. One of the key components required for the production process is a specialized microchip. If the supplier of this microchip faces production issues or experiences delays in delivering the required quantity, it can create a bottleneck in the supply chain. The manufacturing process will be hindered, leading to a delay in the production of finished products. This delay can then ripple through the supply chain, impacting other processes such as packaging, transportation, and ultimately, the delivery of the final products to customers.
The Importance of Efficient Supply Chains
An efficient supply chain is vital for the success of any business. It ensures that products are delivered to customers in a timely manner, reduces costs, and enhances customer satisfaction. A well-functioning supply chain enables businesses to respond quickly to changes in demand, maintain high levels of flexibility, and stay competitive in a rapidly evolving market.
Efficiency in the supply chain can be achieved through various strategies and practices. For instance, implementing advanced technologies such as automation and data analytics can help optimize processes, improve visibility, and enable real-time decision-making. Collaborating closely with suppliers and customers can also enhance coordination and communication, reducing the likelihood of bottlenecks and increasing overall efficiency.
Furthermore, businesses can adopt lean principles and practices to eliminate waste, streamline operations, and improve the flow of goods through the supply chain. This involves identifying and addressing bottlenecks, optimizing inventory management, and continuously monitoring and improving key performance indicators.
In conclusion, understanding supply chain bottlenecks is crucial for businesses aiming to build efficient and resilient supply chains. By identifying and addressing these bottlenecks, businesses can enhance their operational performance, reduce costs, and ultimately deliver value to their customers.
Identifying the Causes of Supply Chain Bottlenecks
Understanding the causes of supply chain bottlenecks is crucial for businesses to proactively address and mitigate them. Let's explore some common causes:
Production Issues
One of the primary causes of supply chain bottlenecks is production issues. These can include machinery breakdowns, labor shortages, or quality control problems. When production stalls or cannot meet the demand, it creates a ripple effect that slows down the entire supply chain.
For example, imagine a manufacturing company that relies on a specific machine to produce their products. If that machine breaks down, it can halt the entire production process. This not only delays the delivery of goods to customers but also disrupts the flow of materials to downstream suppliers. The ripple effect can be significant, causing delays and bottlenecks throughout the supply chain.
Labor shortages can also contribute to production issues. If a company does not have enough skilled workers to operate machinery or perform essential tasks, it can lead to inefficiencies and delays. Additionally, quality control problems can arise if there are issues with the production process or if defective products need to be reworked or discarded.
Transportation Delays
Transportation delays also contribute significantly to supply chain bottlenecks. Factors such as traffic congestion, logistical challenges, or disruptions in shipping can cause delays in the movement of goods. When products are not delivered on time, it can lead to stockouts, increased lead times, and dissatisfied customers.
For instance, imagine a company that relies on a fleet of trucks to transport their products to various distribution centers. If there is heavy traffic congestion on the roads, it can significantly slow down the delivery process. This delay can have a domino effect, causing delays in restocking shelves at retail stores or fulfilling customer orders in a timely manner.
Logistical challenges can also contribute to transportation delays. If a company operates in remote or hard-to-reach areas, it may face difficulties in finding reliable transportation options. Additionally, disruptions in shipping, such as weather-related issues or labor strikes, can further exacerbate transportation delays and create bottlenecks in the supply chain.
Demand Fluctuations
Unpredictable fluctuations in demand can put immense strain on supply chains. Sudden spikes in demand or unexpected downturns can overwhelm businesses and create bottlenecks. Without proper forecasting and planning, businesses may struggle to meet changing customer requirements and maintain a smooth flow of goods.
For example, imagine a company that manufactures seasonal products, such as holiday decorations. During the holiday season, there is a surge in demand for these products. If the company fails to accurately forecast this increased demand and adequately prepare their supply chain, it can lead to bottlenecks. The company may not have enough raw materials, production capacity, or distribution capabilities to meet the sudden spike in orders.
On the other hand, unexpected downturns in demand can also create bottlenecks. For instance, if a company experiences a sudden drop in sales due to economic factors or changing consumer preferences, they may find themselves with excess inventory that cannot be easily sold. This excess inventory can clog up the supply chain and hinder the flow of goods.
Overall, understanding and addressing the causes of supply chain bottlenecks is essential for businesses to maintain a smooth and efficient flow of goods. By proactively identifying and mitigating these issues, companies can minimize disruptions, improve customer satisfaction, and ultimately enhance their overall supply chain performance.
Challenges Posed by Supply Chain Bottlenecks
Now that we understand the causes, let's explore the challenges that supply chain bottlenecks pose:
Impact on Business Operations
Supply chain bottlenecks disrupt normal business operations. They lead to increased lead times, reduced productivity, and lower overall efficiency. Businesses may struggle to fulfill orders, resulting in dissatisfied customers, damaged reputations, and lost opportunities.
For example, when a bottleneck occurs in the manufacturing process, it can cause delays in the production line. This delay can ripple through the entire supply chain, affecting other stages such as packaging, transportation, and distribution. As a result, the business may experience a backlog of orders, leading to frustrated customers and missed sales opportunities.
Furthermore, supply chain bottlenecks can also impact the quality of products or services. When businesses are under pressure to meet demand quickly, they may compromise on quality control measures, leading to defective or subpar products reaching the customers. This can further damage the business's reputation and erode customer trust.
Financial Implications
Bottlenecks in the supply chain often entail additional costs. These can include expedited shipping fees to meet urgent customer demands, overtime pay for employees working extra hours to address the bottleneck, or penalties for failing to meet agreed-upon delivery timelines. These financial implications can strain a business's bottom line and impact profitability.
For instance, when a supply chain bottleneck occurs, businesses may need to pay premium prices for expedited shipping to ensure timely delivery. This can significantly increase transportation costs and eat into the profit margins. Additionally, the need for overtime pay to address the bottleneck can lead to inflated labor costs, further impacting the financial health of the business.
Moreover, supply chain bottlenecks can also result in lost sales and missed revenue opportunities. When customers experience delays or stockouts, they may turn to competitors to fulfill their needs. This loss of business can have long-term financial implications, as customers may switch their loyalty to alternative suppliers, resulting in a decline in market share and revenue.
Customer Satisfaction Concerns
One of the most significant challenges arising from supply chain bottlenecks is the impact on customer satisfaction. Delays and stockouts can lead to frustrated customers who may seek alternative suppliers. This can damage brand loyalty and erode trust in the business.
For example, when a customer places an order and experiences a delay due to a supply chain bottleneck, they may feel let down and dissatisfied with the business. This negative experience can tarnish their perception of the brand and make them hesitant to make future purchases. In today's highly competitive market, where customer experience plays a crucial role, such dissatisfaction can have long-lasting consequences for the business.
Furthermore, supply chain bottlenecks can also affect customer relationships and communication. When businesses are unable to fulfill orders or provide accurate delivery estimates, it can lead to strained relationships with customers. This breakdown in communication can further erode trust and make it difficult to regain customer loyalty.
Strategies to Navigate Supply Chain Bottlenecks
Supply chain bottlenecks can pose significant challenges for businesses, hindering the smooth flow of goods and impacting overall operations. Fortunately, there are several strategies that businesses can implement to effectively navigate these bottlenecks. Let's explore some of these approaches in detail:
Implementing Advanced Planning Systems
One effective strategy to optimize supply chain operations and address bottlenecks is by . These systems leverage data analytics, machine learning, and artificial intelligence to forecast demand, streamline procurement, and improve production scheduling. By adopting these technologies, businesses can proactively identify and address potential bottlenecks before they disrupt operations. For example, by analyzing historical data and market trends, advanced planning systems can help businesses anticipate spikes in demand and adjust their production and inventory levels accordingly.
Furthermore, these systems enable businesses to optimize their transportation routes and logistics, ensuring efficient movement of goods from suppliers to customers. By leveraging real-time data and predictive analytics, businesses can make informed decisions and take proactive measures to prevent bottlenecks. For instance, if a particular transportation route is experiencing congestion or delays, the advanced planning system can suggest alternative routes or modes of transportation to ensure timely delivery.
Diversifying Supplier Networks
Relying on a single supplier or source for critical components or materials can increase the risk of supply chain bottlenecks. To mitigate this risk, businesses can diversify their supplier networks. This involves sourcing from different regions, exploring partnerships with local suppliers, or building strategic alliances to ensure a constant supply of essential inputs.
By , businesses can reduce their dependency on a single source and have alternative options in times of disruptions. For example, if a supplier experiences a production delay or shutdown, having multiple suppliers can help businesses maintain a steady supply of materials or components. Additionally, by sourcing from different regions, businesses can minimize the impact of regional disruptions such as natural disasters or political instability.
Investing in Technology and Automation
Technology and automation play a crucial role in preventing and mitigating supply chain bottlenecks. By leveraging technologies like Internet of Things (IoT), robotics, and big data analytics, businesses can enhance visibility, improve forecasting accuracy, and automate repetitive tasks.
For instance, IoT devices can be used to track and monitor inventory levels in real-time, providing businesses with accurate and up-to-date information about their stock levels. This helps businesses avoid stockouts or overstocking, which can lead to bottlenecks in the supply chain. Additionally, robotics and automation can streamline warehouse operations, reducing the time and effort required to pick, pack, and ship products. This not only improves efficiency but also minimizes the chances of errors or delays.
Furthermore, big data analytics can help businesses identify patterns and trends in their supply chain data, enabling them to make data-driven decisions and optimize their operations. By analyzing historical data, businesses can identify potential bottlenecks and take proactive measures to prevent them. For example, if a particular production process is consistently causing delays, data analytics can help identify the root cause and suggest improvements to streamline the process.
In conclusion, supply chain bottlenecks can pose significant challenges for businesses, impacting their operations and customer satisfaction. However, by understanding the causes, challenges, and implementing effective strategies, businesses can successfully navigate these bottlenecks. By investing in advanced planning systems, diversifying supplier networks, and leveraging technology and automation, businesses can optimize their supply chain operations and ensure a seamless flow of goods. Proactive measures and continuous improvement are key to overcoming the challenges that supply chain bottlenecks present and maintaining a competitive edge in today's dynamic business environment.
Nitro Logistics Team
Logistics Expert
The Nitro Logistics team brings together decades of experience in logistics, fulfillment, and supply chain optimization.
Stay Updated
Get the latest insights in logistics and fulfillment delivered to your inbox.