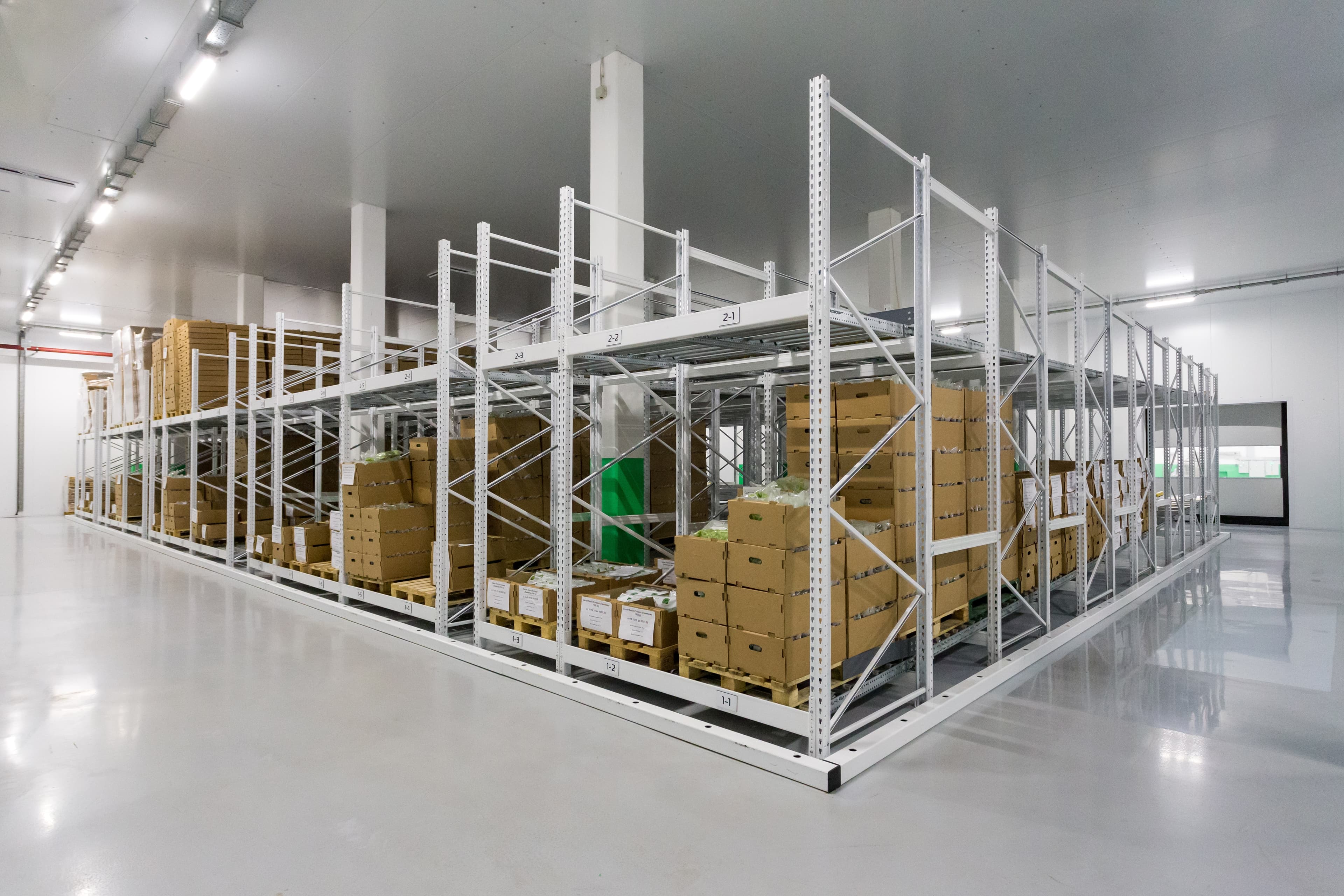
Warehouse Layout and Design: Maximizing Space and Workflow Efficiency
In today's fast-paced business environment, optimizing warehouse operations is crucial for staying competitive. An efficient warehouse layout not only but also enhances workflow efficiency, leading to improved productivity and customer satisfaction. In this article, we will explore the importance of warehouse layout and design, the key elements of an efficient layout, steps to designing a layout, implementing the design, and the role of technology in warehouse operations.
Understanding the Importance of Warehouse Layout and Design
Warehouse layout plays a vital role in the overall efficiency of business operations. It involves the strategic arrangement of storage areas, workstations, aisles, and equipment to create a functional and streamlined workflow. A well-designed layout and reduces congestion, resulting in faster order processing times and fewer errors.
But what exactly makes a warehouse layout effective? Let's delve deeper into the topic to understand its importance and how it impacts business operations.
The Role of Warehouse Layout in Business Operations
A warehouse is a hub of various activities, including receiving, storing, picking, packing, and shipping goods. The layout should support these activities by providing clear pathways for material movement, minimizing bottlenecks, and facilitating smooth transitions between different operational areas. A poorly designed layout can lead to delays, inefficiencies, and increased costs.
Imagine a warehouse where the receiving area is located far away from the storage racks. This layout would require excessive travel time for workers to move goods from the receiving area to the storage area, resulting in wasted time and energy. On the other hand, a well-designed layout would position the receiving area in close proximity to the storage racks, allowing for quick and efficient transfer of goods.
Furthermore, an effective warehouse layout considers the specific requirements of the business. For example, if a company deals with perishable goods, the layout should incorporate temperature-controlled storage areas to . By tailoring the layout to the unique needs of the business, companies can optimize their operations and ensure customer satisfaction.
How Design Impacts Workflow Efficiency
Efficient workflow relies on the logical flow of materials and personnel within the warehouse. A well-designed layout takes into account the sequence of operations, work processes, and traffic patterns. By analyzing these factors, businesses can optimize the placement of storage racks, workstations, and equipment to minimize unnecessary movements and maximize productivity.
For instance, a warehouse that handles a high volume of orders can benefit from a layout that incorporates a pick-and-pack zone close to the shipping area. This arrangement reduces the time required to fulfill orders, as workers can quickly retrieve items from the storage racks, pack them, and send them off for shipping. By strategically placing workstations and equipment, businesses can eliminate bottlenecks and ensure a smooth flow of operations.
Design also plays a crucial role in ensuring the safety of warehouse operations. A well-thought-out layout includes designated walkways, clear signage, and proper lighting to prevent accidents and injuries. By prioritizing safety in the design process, companies can create a secure working environment for their employees.
Moreover, a good warehouse layout allows for scalability and adaptability. As businesses grow and evolve, they may need to accommodate changes in product lines, storage requirements, or operational processes. A flexible layout can easily accommodate these changes, minimizing disruptions and allowing for seamless expansion.
In conclusion, warehouse layout and design are essential factors that significantly impact the efficiency and productivity of business operations. By considering the specific needs of the business, optimizing material flow, and ensuring safety, companies can create a well-designed warehouse layout that maximizes productivity and minimizes costs.
Key Elements of an Efficient Warehouse Layout
An efficient warehouse layout incorporates several key elements that work together to create an organized and productive environment.
When it comes to designing a warehouse layout, there are many factors to consider. One of the most important aspects is space utilization strategies. Effective space utilization is crucial in a warehouse, where every square foot has a value. By employing smart storage solutions such as vertical racking, mezzanine floors, and optimized shelving systems, businesses can make the most of their available space. These space utilization strategies not only maximize storage capacity but also improve accessibility and ease of inventory management. Implementing a systematic inventory management system also helps in maximizing storage efficiency. With an organized and well-utilized space, warehouses can streamline their operations and improve overall productivity.
Another crucial element of an efficient warehouse layout is workflow optimization techniques. An optimized workflow relies on a well-designed layout that minimizes non-value-added activities. Workstations should be strategically placed to minimize travel distance and reduce the number of touches required for order processing. This not only saves time but also reduces the risk of errors and improves overall efficiency. Utilizing continuous improvement techniques, such as Lean Six Sigma, businesses can identify and eliminate bottlenecks, reducing lead times and increasing customer satisfaction. By analyzing the flow of materials, information, and people within the warehouse, businesses can identify areas for improvement and implement changes that enhance productivity.
Furthermore, safety considerations play a vital role in an efficient warehouse layout. Warehouses are often busy and bustling environments, with various types of equipment and machinery in operation. It is essential to design the layout in a way that ensures the safety of employees and minimizes the risk of accidents. This includes providing clear pathways, adequate lighting, and proper signage to guide employees. Additionally, implementing safety protocols and training programs can help create a culture of safety within the warehouse, reducing the likelihood of injuries and disruptions to operations.
In conclusion, an efficient warehouse layout is a combination of space utilization strategies, workflow optimization techniques, and safety considerations. By carefully designing the layout and incorporating these key elements, businesses can create a well-organized and productive warehouse environment. This, in turn, leads to improved operational efficiency, reduced costs, and increased customer satisfaction.
Steps to Designing an Efficient Warehouse Layout
Designing an efficient warehouse layout requires careful planning and consideration. The following steps can guide businesses in creating an optimized layout.
Assessing Your Current Warehouse Layout
Before making any changes, it is essential to understand the strengths and weaknesses of your current layout. Conduct a thorough assessment, considering factors such as workflow, space utilization, safety, and accessibility. Identify areas that require improvement and opportunities for optimization.
During the assessment process, it is important to analyze the flow of goods within the warehouse. This includes evaluating the efficiency of receiving, storage, picking, packing, and shipping processes. By identifying bottlenecks and areas of congestion, you can make informed decisions on how to improve the overall layout.
Additionally, consider the utilization of vertical space in your warehouse. Are you maximizing storage capacity by utilizing mezzanines or high racks? By utilizing vertical space effectively, you can increase storage capacity without expanding the physical footprint of your warehouse.
Planning for Future Growth
Successful businesses anticipate growth and plan their layouts accordingly. Consider future expansion plans, changes in product lines, and any technological advancements that may impact your operations. Design your layout with flexibility in mind, allowing for easy scalability and efficient reconfiguration as your business evolves.
When planning for future growth, it is important to consider the impact of automation and robotics on your warehouse operations. As technology continues to advance, integrating automated systems into your layout can significantly increase efficiency and productivity. This may include automated conveyor systems, robotic picking and packing, or even autonomous forklifts.
Furthermore, think about the potential for implementing advanced inventory management systems. These systems can provide real-time visibility into your inventory, allowing for better demand forecasting and inventory control. By incorporating such systems into your layout, you can optimize storage space and reduce the risk of stockouts or overstocking.
Lastly, consider the impact of e-commerce on your warehouse layout. With the rise of online shopping, warehouses are increasingly becoming fulfillment centers. This shift in the retail landscape requires careful planning to accommodate the high volume of small, individual orders. Designing a layout that supports efficient order picking and packing processes is crucial to meet customer expectations for fast and accurate order fulfillment.
Implementing Your Warehouse Design
Once the design phase is complete, it's time to implement the changes and transition to the new layout.
Implementing a new warehouse design is an exciting and challenging endeavor. It involves more than just rearranging shelves and equipment; it requires careful planning, coordination, and effective communication. The success of the implementation phase can greatly impact the overall efficiency and productivity of your warehouse.
Before diving into the implementation process, it is essential to develop a well-defined plan. This plan should outline the specific steps, timelines, and resource allocation needed to execute the new layout successfully. By having a clear roadmap, you can ensure that everyone involved is on the same page and working towards a common goal.
Transitioning to a New Layout
Transitioning to a new warehouse layout can be a complex process. It is crucial to have a well-defined plan, including timelines, resource allocation, and regular communication with the warehouse staff. Proper training and support during the transition phase ensure a smooth adoption of the new layout.
One of the key factors in a successful transition is effective communication. Regularly updating the warehouse staff about the progress of the implementation, addressing any concerns or questions they may have, and providing them with the necessary training and support will help ease the transition process. Additionally, involving the staff in the decision-making process and seeking their input can foster a sense of ownership and commitment to the new layout.
Another important aspect of transitioning to a new layout is ensuring that the necessary resources are allocated correctly. This includes not only physical resources such as equipment and materials but also human resources. Assigning dedicated personnel to oversee the implementation process, monitor progress, and address any issues that may arise is essential for a smooth transition.
Maintaining Efficiency Over Time
Efficiency is not a one-time achievement; it requires continuous efforts. Regularly review and analyze the performance of your warehouse layout. Seek feedback from employees and keep an eye on industry trends and best practices. Implement changes as necessary to maintain or enhance efficiency over time.
Once the new layout is in place, it is important to monitor its performance and make adjustments as needed. Regularly reviewing key performance indicators such as order fulfillment time, inventory accuracy, and picking accuracy can provide valuable insights into the effectiveness of the new layout. Additionally, seeking feedback from warehouse staff about their experience with the new design can help identify any areas for improvement.
Staying up to date with industry trends and best practices is also crucial for maintaining efficiency over time. The logistics and warehousing industry is constantly evolving, with new technologies and methodologies emerging regularly. By staying informed and implementing relevant changes, you can ensure that your warehouse remains competitive and efficient.
In conclusion, implementing a new warehouse design requires careful planning, effective communication, and continuous improvement. By following these guidelines, you can successfully transition to a new layout and maintain efficiency over time, ultimately optimizing your warehouse operations and maximizing productivity.
The Role of Technology in Warehouse Layout and Design
Technology plays an increasingly vital role in warehouse operations, revolutionizing the way layouts are designed and managed. With the advent of advanced software solutions and automation technologies, businesses now have the opportunity to optimize their warehouse layouts for maximum efficiency and productivity.
Warehouse Management Systems (WMS)
A Warehouse Management System (WMS) is a software solution that centralizes and automates various warehouse processes, including inventory tracking, order fulfillment, and workforce management. By implementing a WMS, businesses can streamline their operations and gain real-time visibility into their inventory levels and movement.
With the ability to track inventory accurately, businesses can make informed decisions about warehouse layout and design. For example, they can identify fast-moving products and allocate more space for their storage, while optimizing the placement of slower-moving items to maximize space utilization.
The Impact of Automation and Robotics
Automation and robotics have transformed warehouse operations, leading to increased accuracy, speed, and efficiency. Technologies such as Automated Guided Vehicles (AGVs), robotic picking systems, and warehouse drones are revolutionizing the way layouts are designed and utilized.
AGVs, for instance, can navigate through the warehouse autonomously, transporting goods from one location to another. This eliminates the need for manual labor and reduces the risk of human errors. Robotic picking systems, on the other hand, can swiftly and accurately pick items from shelves, improving order fulfillment speed and accuracy.
By embracing these technologies, businesses can achieve higher levels of space optimization and workflow efficiency. For example, AGVs can navigate through narrow aisles, allowing for narrower storage lanes and thus increasing the overall storage capacity of the warehouse. Robotic picking systems can also be integrated with WMS, enabling seamless coordination between inventory management and order fulfillment processes.
By understanding the importance of warehouse layout and design, implementing efficient layouts, and leveraging technological advancements, businesses can maximize space utilization and enhance workflow efficiency. A well-designed warehouse layout sets the foundation for streamlined operations, improved productivity, and ultimately, a competitive advantage in the market.
Nitro Logistics Team
Logistics Expert
The Nitro Logistics team brings together decades of experience in logistics, fulfillment, and supply chain optimization.
Stay Updated
Get the latest insights in logistics and fulfillment delivered to your inbox.