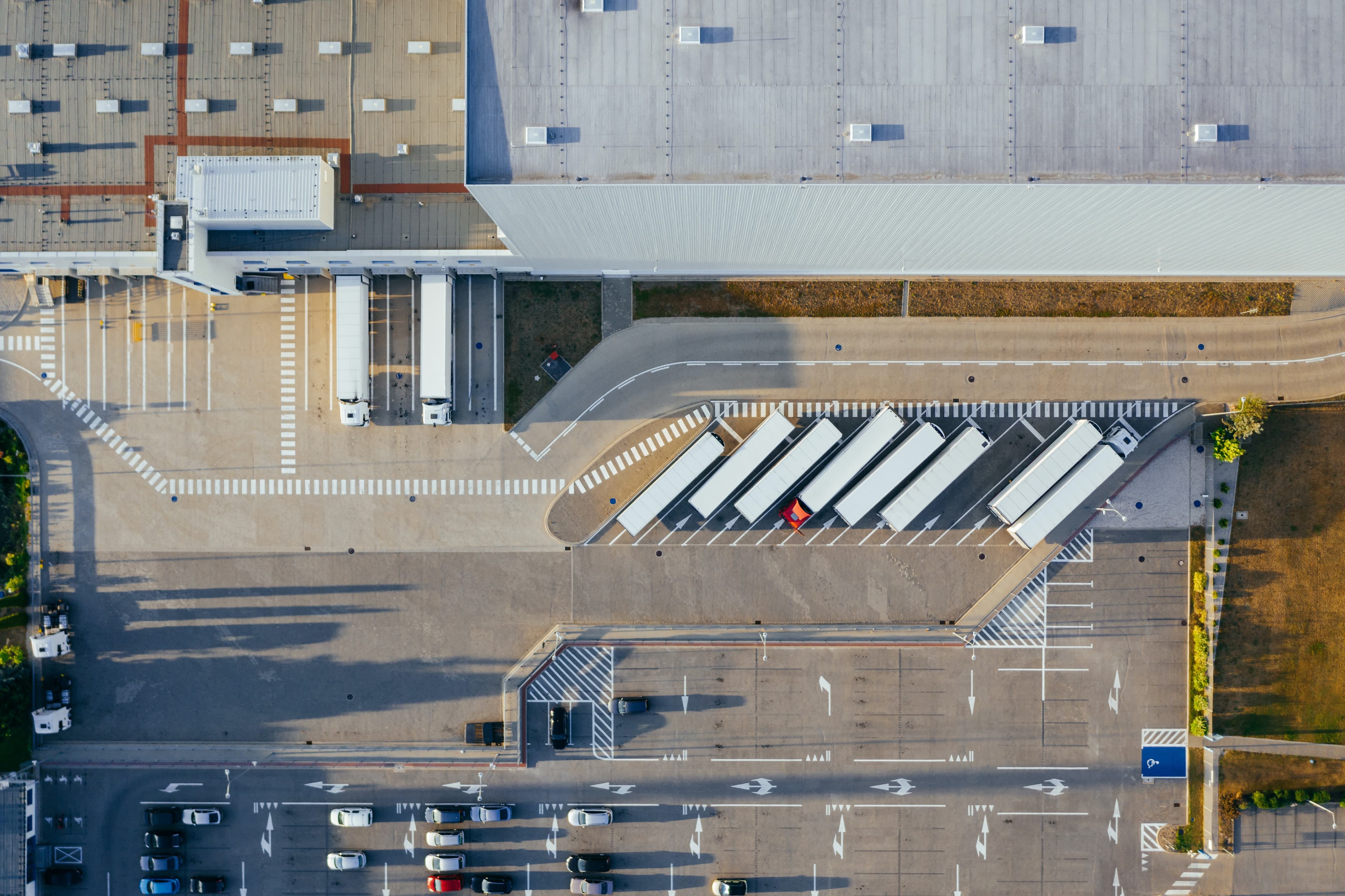
Zone Picking: Guide, Benefits, and How it Works in the Warehouse
Warehouse operations play a crucial role in the overall success of a business, and is a key driver of customer satisfaction. One method that has gained popularity in recent years is zone picking. This article will serve as a comprehensive guide to zone picking, exploring its benefits and explaining how it works in the warehouse.
Understanding the Concept of Zone Picking
Before diving into the specifics of zone picking, it's important to have a clear definition of what it entails.
Zone picking is a warehousing strategy where the picking process is divided into distinct zones or areas within the warehouse. Each zone is assigned to specific warehouse workers who are responsible for fulfilling orders within their designated area.
By implementing zone picking, companies can and . This strategy allows for greater efficiency, accuracy, and speed in picking and packing orders.
Definition of Zone Picking
Zone picking is a methodical approach to order fulfillment that involves dividing the warehouse into different zones or areas. Each zone is assigned to a specific group of workers, known as pickers, who are responsible for picking and packing items within their designated area.
The goal of zone picking is to improve productivity and reduce order processing time by breaking down the picking process into smaller, more manageable tasks. By assigning specific zones to workers, they can become familiar with the layout and inventory of their area, leading to increased efficiency and accuracy.
The Basic Principles of Zone Picking
The essence of zone picking lies in its division of labor. Instead of having each worker responsible for picking items for an entire order, zone picking allows for specialization and increased efficiency. Each worker focuses solely on their assigned zone, becoming experts in the products and layout of that area.
Furthermore, zone picking promotes parallel processing, as multiple workers can simultaneously pick items from different zones. This contributes to a significant reduction in order fulfillment time. With the ability to work in parallel, the picking process becomes more streamlined, allowing for a higher volume of orders to be processed within a shorter timeframe.
Another key principle of zone picking is the concept of batch picking. In this approach, pickers are assigned to retrieve multiple items for different orders within their zone at once. This minimizes the need for repeated trips to the same location and maximizes efficiency by consolidating picking tasks.
Zone picking also enables better inventory control and accuracy. By assigning specific workers to each zone, it becomes easier to track and monitor inventory levels within those areas. This ensures that stock is replenished in a timely manner, reducing the risk of stockouts and improving overall customer satisfaction.
In addition to these principles, zone picking can be further enhanced through the use of technology. Warehouse management systems (WMS) and barcode scanning devices can be integrated to provide real-time inventory updates, optimize pick routes, and improve order accuracy.
In conclusion, zone picking is a warehousing strategy that divides the picking process into distinct zones or areas within the warehouse. By assigning specific zones to workers, promoting parallel processing, and utilizing batch picking, companies can achieve higher efficiency, accuracy, and productivity in their order fulfillment operations.
The Mechanism of Zone Picking in Warehouses
Now that we have a solid understanding of the concept, let's explore how zone picking works in practice within warehouses.
Zone picking is a highly efficient method used in warehouses to fulfill customer orders. It involves dividing the warehouse into different zones and assigning specific workers to each zone. This division allows for streamlined operations and increased productivity.
The Role of Warehouse Workers in Zone Picking
Warehouse workers are at the heart of the zone picking process. They play a vital role in ensuring that orders are accurately picked and ready for shipment.
Each worker is assigned a specific zone, which could be based on product categories, customer segments, or any other logical division. This allocation is done strategically to optimize the picking process and minimize the time taken to fulfill orders.
Once assigned to a zone, workers become familiar with the location of products within their zone. They develop an intimate knowledge of the layout, making it easier for them to navigate through the warehouse and locate items efficiently.
As workers gain experience in their designated zones, they become even more proficient in their tasks. They can quickly identify the most efficient routes, locate items with ease, and minimize errors. This expertise significantly contributes to the overall efficiency and accuracy of the zone picking process.
The Process of Zone Picking
Once an order is received, it goes through a series of steps before it is ready for shipment. The process begins with the division of the order into individual items or SKU (Stock Keeping Unit) requirements.
Based on the availability of the items, the order is then allocated to the respective zones. This allocation is carefully done to ensure that each zone receives the items it needs to fulfill the order.
Warehouse workers, within their assigned zones, play a crucial role in retrieving the items required for the order. They utilize various picking methods to ensure accuracy and efficiency. One such method is the use of pick-to-light systems, where workers are guided by illuminated indicators to the correct location of each item. Another method involves the use of handheld devices that provide workers with real-time information and directions.
Once the items are picked, they are consolidated and prepared for packing and shipping. This involves careful inspection to ensure that the correct items have been retrieved and that they are in optimal condition for delivery.
Zone picking not only improves the speed and accuracy of order fulfillment but also enhances the overall organization and workflow within the warehouse. By dividing the warehouse into zones and assigning dedicated workers to each zone, the process becomes more streamlined, reducing the chances of errors and delays.
In conclusion, zone picking is a highly effective method used in warehouses to optimize order fulfillment. It relies on the expertise of warehouse workers and strategic allocation of zones to ensure efficient and accurate picking. By understanding the mechanism of zone picking, warehouses can enhance their operations and provide customers with timely and error-free deliveries.
The Advantages of Implementing Zone Picking
The use of zone picking offers several benefits for warehouses looking to optimize their order fulfillment process.
Zone picking is a method of order fulfillment that involves breaking down the picking process into specialized zones. Each zone is assigned to a specific worker or group of workers, who are responsible for picking items only within their designated area. This approach brings about a range of advantages that can greatly improve the efficiency and accuracy of the order fulfillment process.
Efficiency and Productivity Gains
One of the primary advantages of zone picking is the significant boost in efficiency and productivity. By breaking down the picking process into specialized zones, workers can focus on their specific areas, resulting in faster and more accurate picking.
When workers are assigned to a specific zone, they become experts in that area. They develop a deep understanding of the layout, organization, and characteristics of the products within their zone. This familiarity allows them to navigate the zone quickly and efficiently, locating and picking items with ease.
Furthermore, zone picking enables parallel processing, which means multiple workers can pick orders simultaneously in different zones. This parallel processing capability allows for a higher throughput of orders, reducing bottlenecks and ensuring timely fulfillment. With each worker focused on their assigned zone, the overall picking process becomes streamlined and optimized.
Improved Order Accuracy
Zone picking minimizes the risk of errors in order fulfillment. With workers becoming experts in their assigned zones, they develop a deep understanding of the products they handle. This knowledge reduces the chances of picking the wrong item and improves overall order accuracy.
When workers are familiar with the products in their zone, they can easily identify any discrepancies or anomalies. They can quickly spot incorrect items, damaged goods, or expired products, ensuring that only the correct and high-quality items are picked for each order.
In addition, zone picking reduces the likelihood of mixing up similar-looking products. With workers focused on a specific range of items, they become attuned to the subtle differences between products, such as variations in packaging or labeling. This attention to detail significantly reduces the risk of picking the wrong item, leading to improved order accuracy and customer satisfaction.
Overall, the implementation of zone picking in warehouses can bring about significant efficiency and accuracy gains. By breaking down the picking process into specialized zones and assigning workers accordingly, warehouses can optimize their order fulfillment operations, resulting in faster, more accurate, and more reliable order processing.
Potential Challenges in Zone Picking
While zone picking brings numerous benefits, it is essential to address potential challenges that may arise during implementation.
Zone picking, a popular order fulfillment method in warehouses, offers several advantages such as increased productivity, reduced travel time, and improved order accuracy. However, like any operational change, it is important to consider and overcome potential challenges to ensure a successful implementation.
Training and Staffing Considerations
Instituting zone picking requires proper training and support for warehouse workers. They need to familiarize themselves with the new processes and learn how to navigate their respective zones efficiently. Adequate staffing levels must also be maintained to ensure smooth operations within each zone.
Training programs should be designed to provide workers with a comprehensive understanding of zone picking techniques, including how to identify and pick items within their assigned zones. This training should also cover safety protocols and best practices to minimize the risk of accidents or injuries.
Furthermore, ongoing support and feedback from supervisors and managers are crucial to address any concerns or challenges that workers may encounter during the transition period. Regular meetings and performance evaluations can help identify areas for improvement and ensure that employees feel supported and motivated.
Dealing with Varied Inventory Sizes
Warehouses often handle a diverse range of products, with variations in size, weight, and fragility. It is crucial to consider these factors when implementing zone picking to ensure that each zone is appropriately equipped to handle different inventory requirements. Proper shelving, equipment, and storage solutions are essential for facilitating smooth operations.
For example, zones that handle small and lightweight items may require specialized shelving units with smaller compartments to maximize storage capacity and minimize the risk of damage. On the other hand, zones that handle larger or heavier items may need sturdy pallet racks or forklifts to ensure safe and efficient movement.
Additionally, implementing a robust inventory management system can help warehouse managers track and categorize products based on their size and weight. This information can then be used to allocate the appropriate zones for each item, ensuring that the picking process is streamlined and optimized.
Moreover, regular maintenance and inspections of equipment and storage solutions are crucial to identify any potential issues or hazards. By addressing these issues promptly, warehouse managers can prevent disruptions in the picking process and maintain a safe working environment.
In conclusion, while zone picking offers numerous benefits, it is important to address potential challenges during implementation. By providing proper training and support to warehouse workers and considering the varied inventory sizes, warehouses can overcome these challenges and maximize the efficiency and effectiveness of their zone picking operations.
Tips for Successful Zone Picking Implementation
To ensure a successful zone picking implementation, there are a few key factors to consider.
Choosing the Right Warehouse Layout
Designing an efficient warehouse layout is critical for optimal zone picking performance. The layout should ensure logical product placement within each zone, minimizing travel time between items and improving overall picking speed.
Leveraging Technology in Zone Picking
Advancements in technology have greatly enhanced zone picking processes. Implementing pick-to-light systems, handheld devices, or even automated robots can increase accuracy, speed, and productivity in the warehouse. Exploring and adopting these technological solutions can significantly benefit zone picking operations.
In conclusion, zone picking is a powerful warehousing strategy that can revolutionize order fulfillment processes. By dividing the picking process into specialized zones and leveraging the expertise of warehouse workers, businesses can experience increased efficiency, improved order accuracy, and a streamlined workflow. However, it is crucial to address potential challenges and implement best practices to ensure successful zone picking implementation. With the right approach, businesses can reap the rewards of this innovative order fulfillment methodology.
Nitro Logistics Team
Logistics Expert
The Nitro Logistics team brings together decades of experience in logistics, fulfillment, and supply chain optimization.
Stay Updated
Get the latest insights in logistics and fulfillment delivered to your inbox.